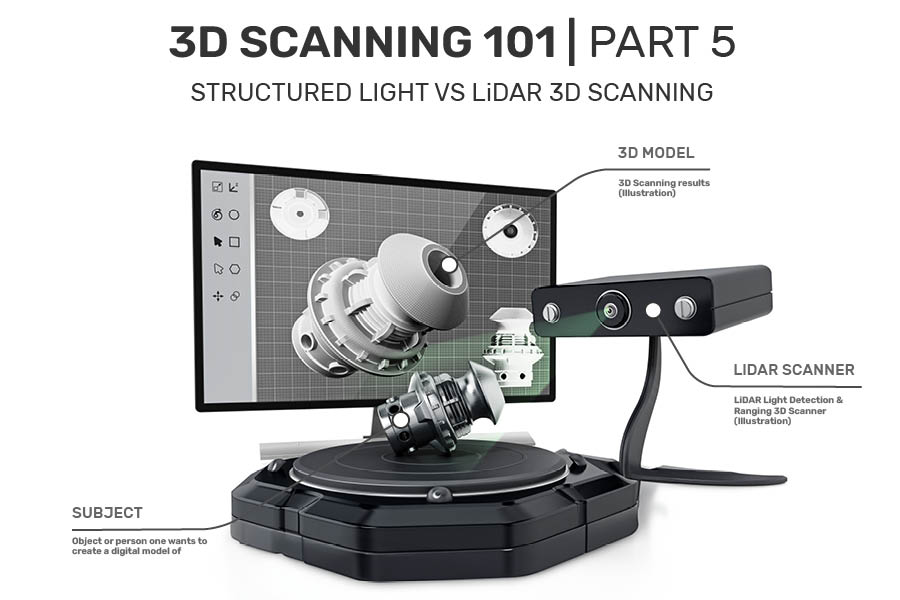
Part 5: Structured Light VS LiDAR 3D Scanning
Contents
- What is LiDAR 3D Scanning?
- Difference between LiDAR and LASER
- Structured Light VS LiDAR
- Advantages of Structured Light
- Ideal Applications Structured Light
- Advantages of LiDAR
- Disadvantages of LiDAR
- Ideal Applications LiDAR
- Conclusion
Introduction
What is LiDAR 3D Scanning? What are the differences between LiDAR and Laser 3D scanning? What are the advantages and disadvantages of structured light 3D scanning over Lidar and some of the best use cases for each? These are just some of the questions and more we will be answering in part 5 of our ongoing series “3D Scanning 101: Structured Light VS LiDAR”.
1. What is LiDAR 3D Scanning
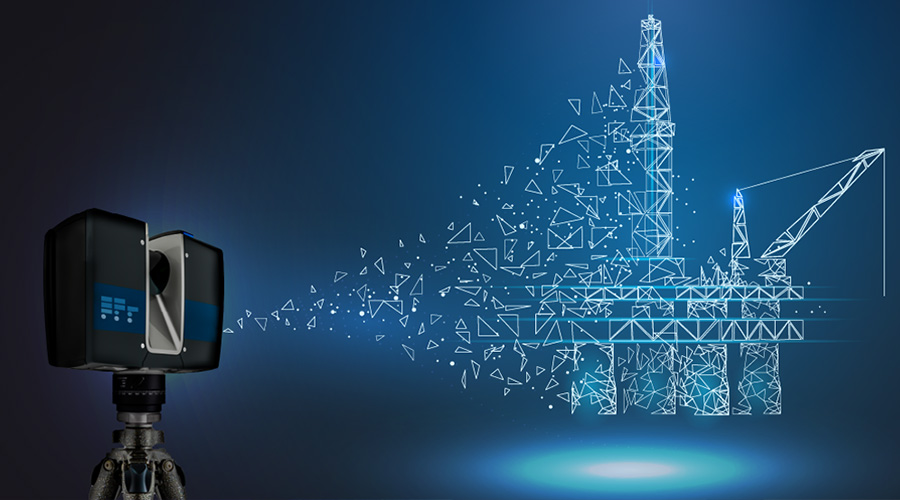
A LiDAR 3D scanner is a device that is used to capture three-dimensional objects and space based on LiDAR technology. It can simultaneously emit multiple laser beams to measure the distance between the sensor and the object.
LiDAR 3D scanning is akin to casting a net of laser light across a scene. This technology shoots rapid pulses of laser light at a surface and waits for each pulse to return. Like timing a fast-paced echo in a vast canyon, LiDAR measures the time it takes for these light pulses to bounce back. These time measurements are then converted into distance readings, painting a 3D picture of the area.

This installment aims to unravel the advantages and disadvantages of each, providing clarity on their best use cases and situations.
2. Difference between LiDAR and LASER
For more on the basics of structured light 3D scanning; see part 1 in our 3D Scanning 101 series Basics of Structured Light
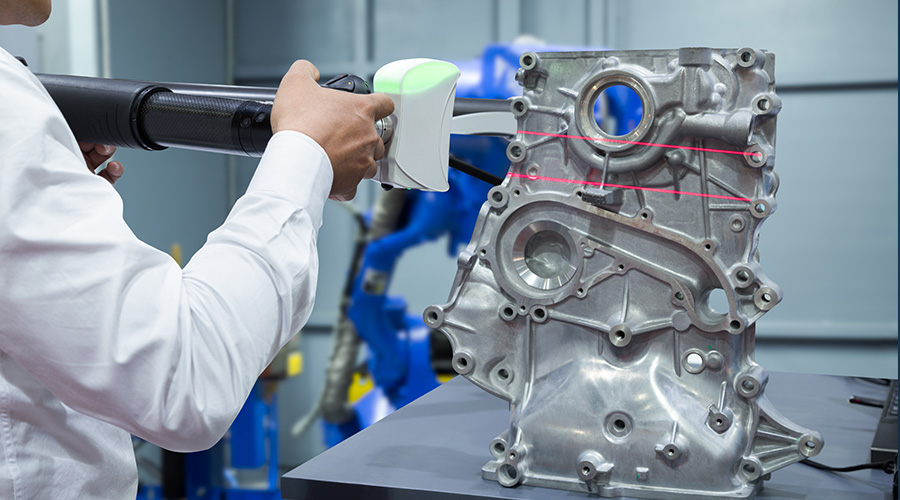
Are LiDAR and laser scanning the same technology? This is a question that many ask, and a large portion of people believe that they are one and the same but believe it or not; they are not the same.
A LASER is a device that produces monochromatic beams of light.
- Laser is a device
- Laser doesn’t use LiDAR
LiDAR measures using penetrating LASER light pulses.
- LiDAR is a technology
- LiDAR uses Lasers
LASER: Laser stands for “Light Amplification by Stimulated Emission of Radiation” and refers to devices that work on this principle to generate and amplify light.
Many of the products we use daily rely heavily on lasers. Laser technology is used in Blu-Ray and DVD players to read data from the disks. Barcode scanners process data using lasers. The use of lasers for surgical treatments like Lasik eye surgery is also commonplace. Cutting, engraving, drilling, and marking are all common uses of lasers.
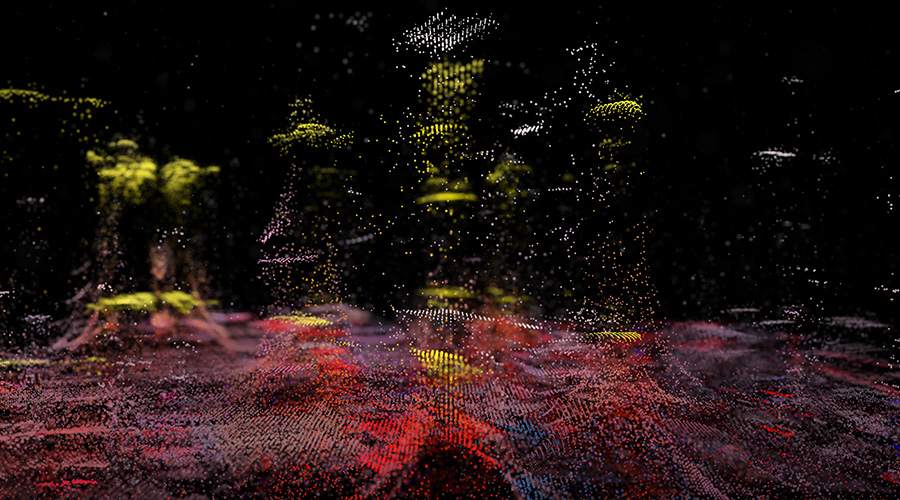
LiDAR: LiDAR stands for “Light Detection And Ranging”, a method of determining the range (distance) between an object and a receiver by use of lasers.
LIDAR, on the other hand, is a technique or a process, whereas the laser is a device. In the Architecture, Engineering, and Construction (AEC) industry, LiDAR technology is used as a 3D laser scanner for buildings to scan buildings and transform them into as-built 3D BIM models.
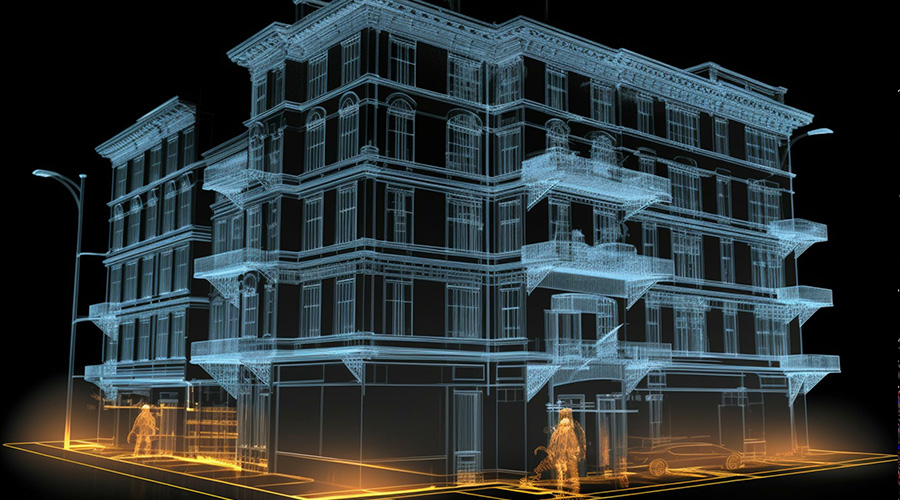
LiDAR works by measuring the light that will be reflected back to the scanner. Following that, the distance between two points is determined using the speed of light. As a result, the digital depiction of the measured places evaluates the entire environmen
3. Structured Light VS LiDAR
The landscape of 3D scanning technology has seen significant advancements over the years, with Structured Light 3D Scanning and Light Detection and Ranging (LiDAR) emerging as two of the most prominent technologies. Each offers unique benefits and challenges, making them suitable for different applications.
However, when it comes to applications requiring high-precision and detail, Structured Light often emerges as the superior choice. Let’s explore the advantages and disadvantages of Structured Light 3D scanning, demonstrating why it often outperforms LiDAR in many but not all scenarios.
4. Advantages of Structured Light
Higher Resolution & Detail
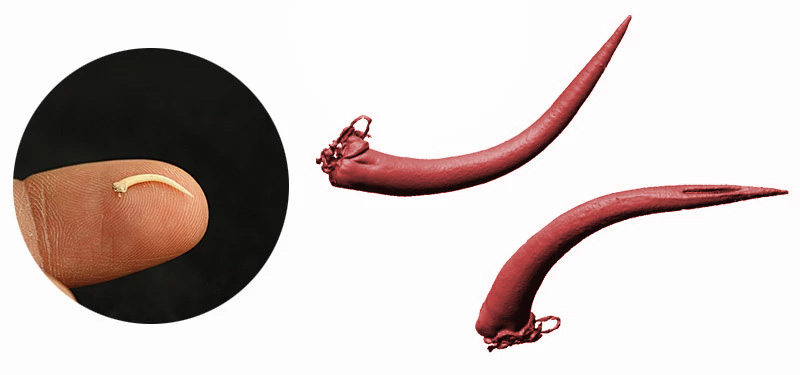
Intricate Data Capture: Structured Light scanners capture finer more intricate details, making them ideal for applications requiring high-resolution scans.
Surface Texture & Color: Apart from geometrical data, Structured Light can capture surface texture and color, providing richer data and more realistic models compared to the often texture-less models produced by LiDAR.
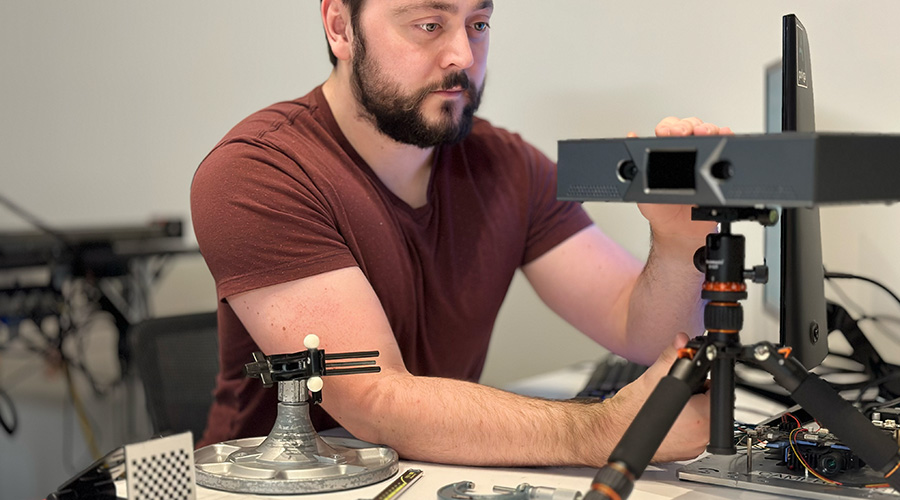
Accuracy & Consistency
Precise Measurements: Structured Light systems generally offer more accurate measurements, especially in cases like quality control and reverse engineering.
Consistent Performance: Unlike LiDAR, which can be sensitive to ambient light and surface reflectivity, Structured Light provides consistent results across various conditions.
Efficiency & Speed
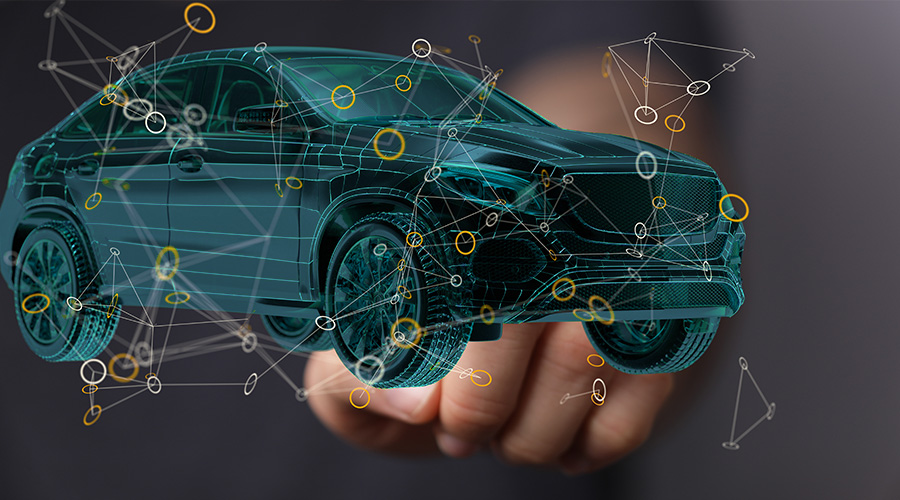
Rapid Data Collection: Structured Light scanning is typically faster in capturing the complete profile of an object due to its ability to project and cycle through complex patterns to capture thousands of points simultaneously.
Reduced Post-Processing Time: The data acquired is often closer to a finished model, requiring less post-processing time.
Versatility
Adaptable for Different Sizes: Structured Light systems can be adapted for scanning small objects (like industrial components) to larger items (such as automotive parts) with advanced models such as the Carbon X.
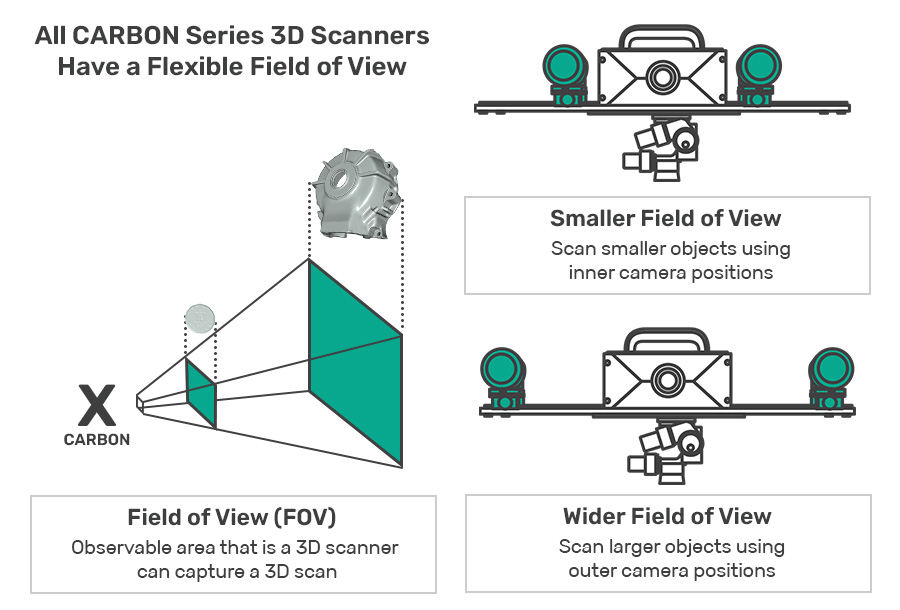
Multiple Scans & Stitching: For large objects, multiple scans from different angles can be stitched together. This approach requires precision and can be time-consuming but results in comprehensive and detailed models.
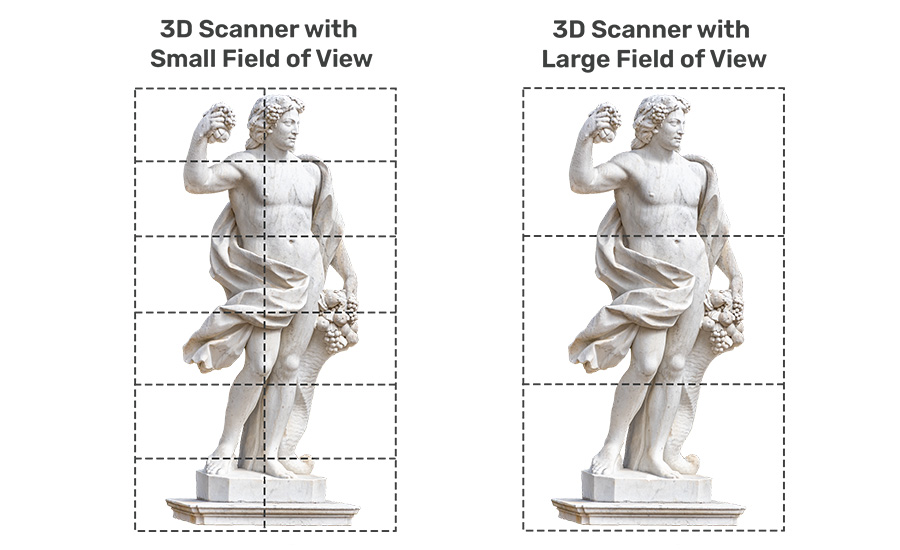
Safety & Usability
Safe for Biological Subjects: Structured Light is safe for scanning people and animals, as it involves no laser exposure.
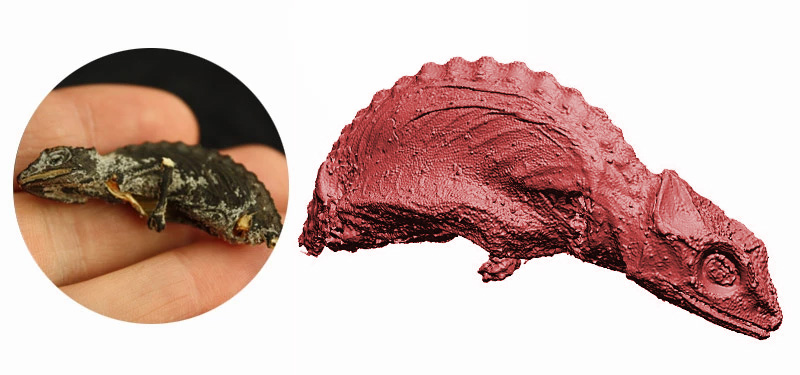
User-Friendly These systems are often more straightforward to set up and operate, making them accessible to a broader range of users.
Costs for High Precision: High-resolution structured systems are significantly more cost-effective. Systems typically offer significantly better performance than comparably priced LiDAR and LASER systems.
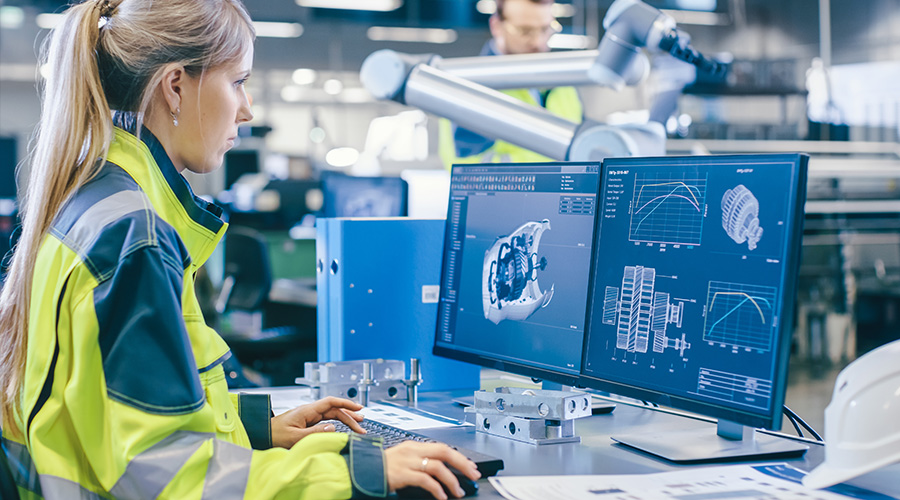
5. Ideal Applications – Structured Light
Manufacturing & Design: For precision engineering, quality control, and reverse engineering.
Cultural Heritage & Archaeology: In the digitization of artifacts where detail and texture are paramount.
Medical & Dental: A non-destructive and non-intrusive method perfect for creating detailed prosthetics or in planning surgical procedures.
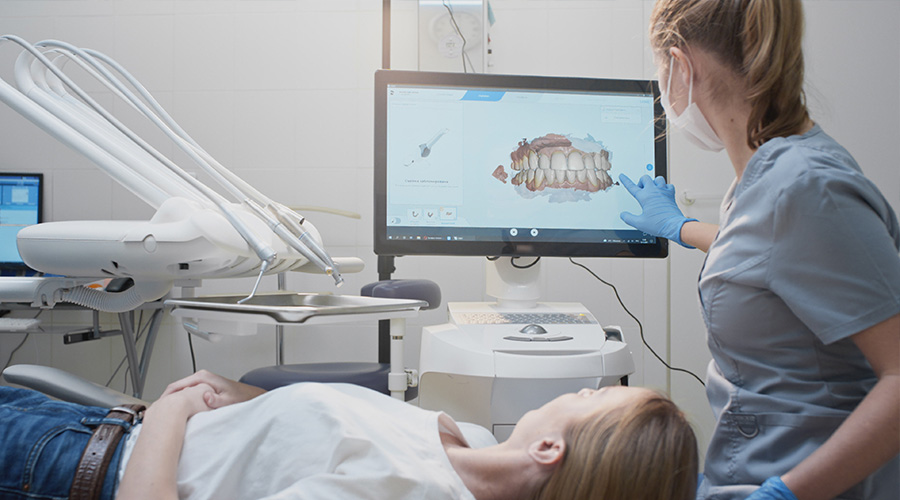
For more best case uses and real-world applications of structured light; read part 2 of our 3D Scanning 101 series, “Real World Applications of Structured Light“.
6. Advantages of LiDAR
Large Area Coverage: LiDAR can cover large areas quickly, making it ideal for aerial or outdoor scans. It is particularly effective for topographical surveys, urban planning, and mapping large environments.
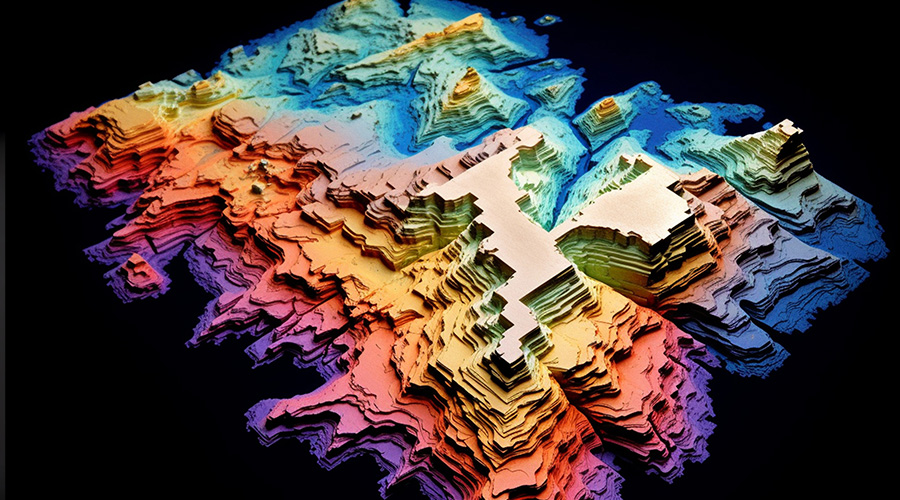
Safety Distance: A LiDAR scanner can measure the hazardous areas where people cannot enter since it can measure at a distance. This feature keeps personnel out of danger and avoids accidental injury.

Obstacle Penetration: It can capture data in challenging terrains such as dense forest, penetrating through obstructions like trees and brush.
Aerial Speed: Airborne LiDAR systems can scan vast areas rapidly, which is much faster compared to the relatively slower process of structured light scanning over large distances.
7. Disadvantages of LiDAR
Lower Resolution & Color: LiDAR is typically less capable of capturing the minute details of an object including color and texture.
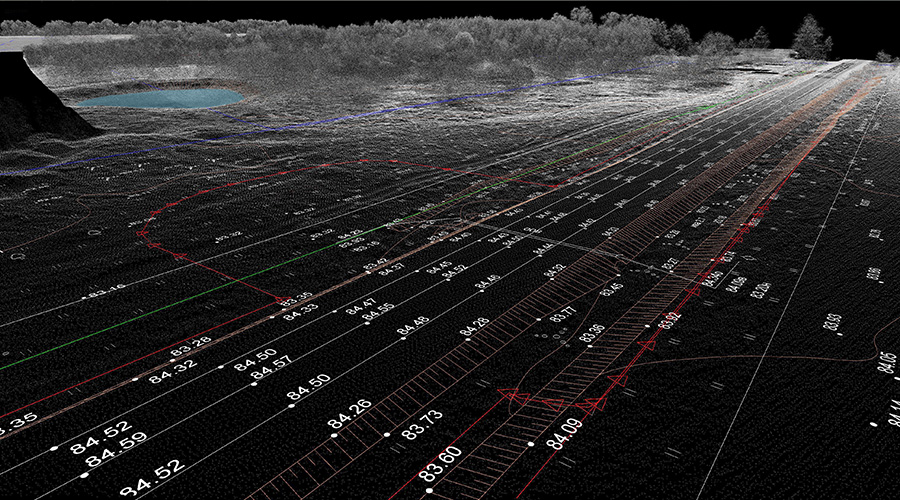
Data Processing: Handling the massive data sets generated by LiDAR can be complex, time-consuming and resource-intensive; adding to the overall costs.
Higher Costs for High Precision: High-resolution LiDAR systems can be significantly more expensive, sometimes costing upwards of $100,000. Aerial systems may cost even more with higher complexity and operating costs.
8. Ideal Applications for LiDAR

Autonomous Vehicles: LiDAR serves as the eyes of autonomous vehicles, providing a 360-degree view of their surroundings. Mounted atop autonomous vehicles, LiDAR systems emit a flurry of laser beams, creating a live, three-dimensional map of the area.
Environmental Monitoring: LiDAR 3D scanning can monitor various types of large scale natural landscapes to capture change, deformation analysis, hazard assessment, structural and infrastructure monitoring.
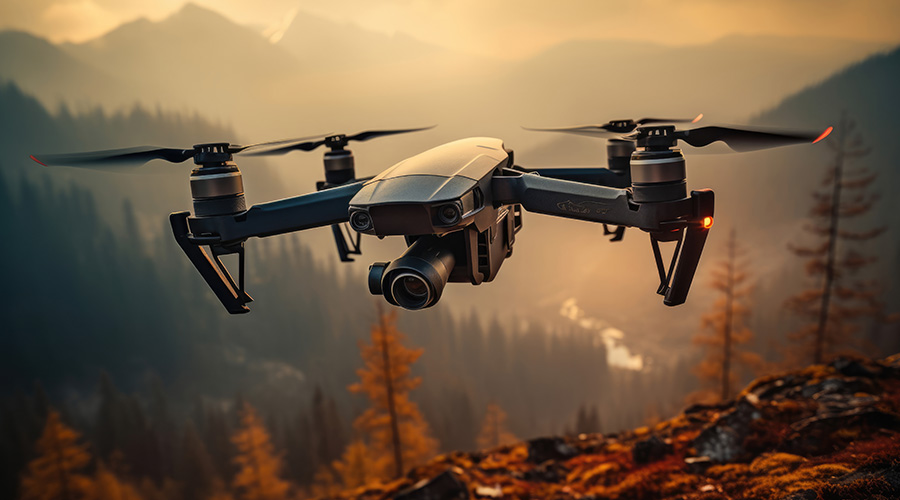
Geological Survey: A geological survey is the systematic investigation of the geology beneath a given piece of ground for the purpose of creating a geological map or model made possible by LiDAR’s ability to penetrate certain obstacles.
Forestry & Agriculture: LiDAR 3D scanning can analyze forests or orchards to extract relevant data of trees and brush in artificial, natural, agricultural applications for yield, growth and health. LiDAR’s penetration capabilities are especially useful in such cases.
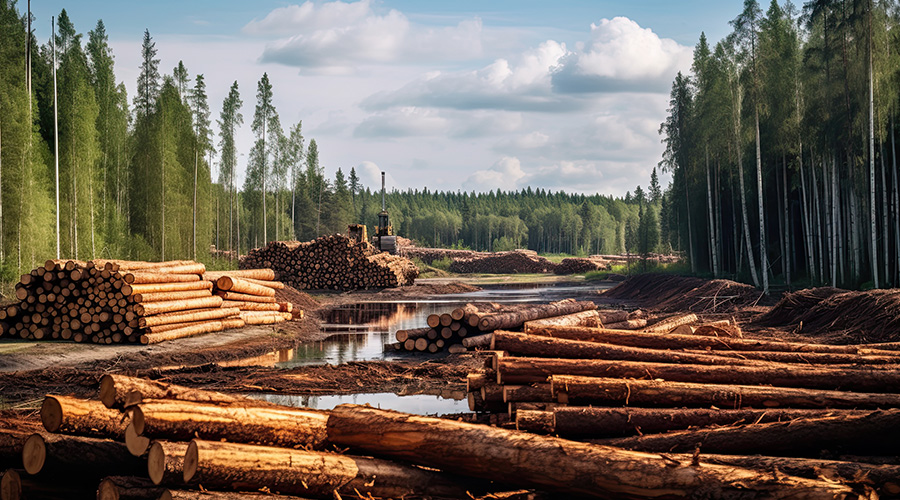
9. Conclusion
While LiDAR excels in the above areas, structured light scanning is more suitable for applications requiring high precision and detail on a smaller scale, such as industrial inspection, quality control, 3D modeling, and cultural heritage preservation.
It’s important to choose the technology based on the specific requirements of the project, considering factors like the environment, scale, and level of detail needed. Polyga, for instance, specializes in structured light 3D scanning solutions tailored for various applications including industrial inspection, quality assurance, and 3D modeling, offering high accuracy and detail for smaller-scale objects.
While LiDAR has its strengths, especially in large-scale outdoor mapping, Structured Light shines in scenarios where detail and accuracy cannot be compromised.
Understanding the strengths and limitations of each technology is crucial in selecting the right tool for your scanning needs, ensuring both efficiency and accuracy in data collection and analysis.
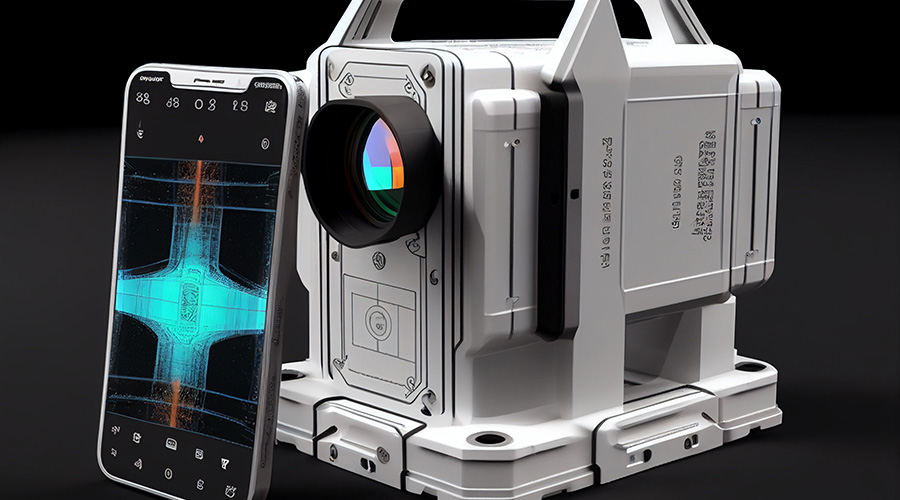
Remember, the landscape of 3D scanning technology is ever-evolving, and staying informed about the latest developments is crucial in making the best choice for your scanning needs.
For more insights into structured light 3D scanning, visit Polyga’s 3D Scanning Learning Center.
Further Reading
- Part 1 – 3D Scanning 101: Basics of Structured Light
- Part 2 – 3D Scanning 101: Real World Applications of Structured Light
- Part 3 – 3D Scanning 101: Size Limitations of Structured Light
- Part 4 – 3D Scanning 101: Structured Light VS LASER
- Part 5 – 3D Scanning 101: Structured Light VS LiDAR
I hope that this article is helpful to you on your 3D scanning journey.
And, if you have any other questions about what type of scanner is right for your project,
feel free to send them to our sales team at sales@polyga.com, and they will be happy to help.
Best regards,
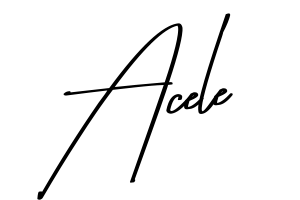
Ace Le
Polyga Inc.
Vancouver, British Columbia, Canada
Email: contact@polyga.com
Website: Polyga.com