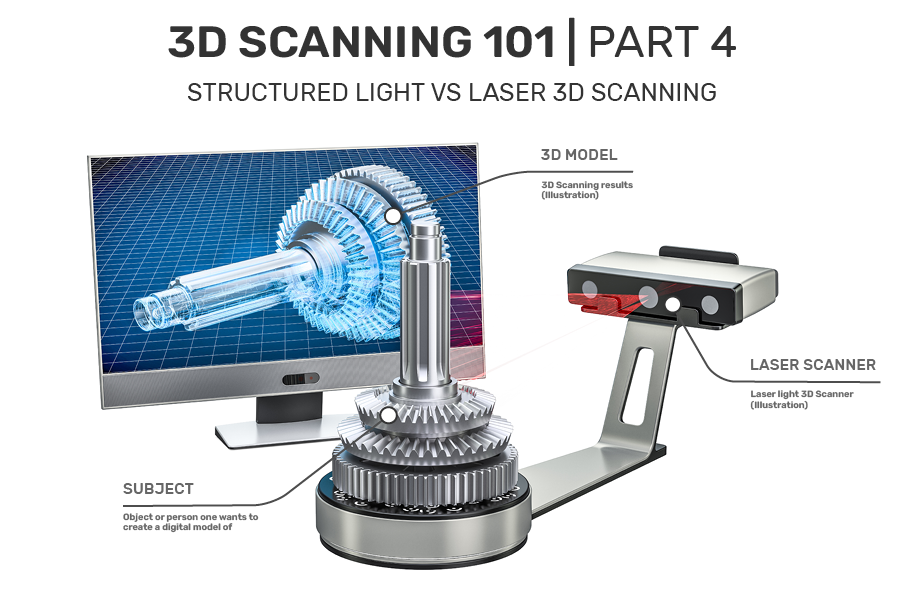
Structured Light Versus Laser 3D Scanning
Introduction
Welcome back to our ongoing “3D Scanning 101” series! In Part 4, we’re diving into a much-debated topic in the 3D scanning community: Structured Light vs. Laser 3D Scanning.
What are the advantages of structured light 3d scanning? What are the advantages of laser 3D scanning? What are the disadvantages? Both technologies have become staples in how we capture and digitize the objects. Often similar in appearance yet cater to different needs and applications.
This installment aims to unravel the advantages and disadvantages of each, providing clarity on their best use cases and situations.
Contents
- Spotlight on Structured Light 3D Scanning
- Structured Light Key Takeaway
- Shining a Light on Laser 3D Scanning
- Laser Key Takeaway
- Conclusion
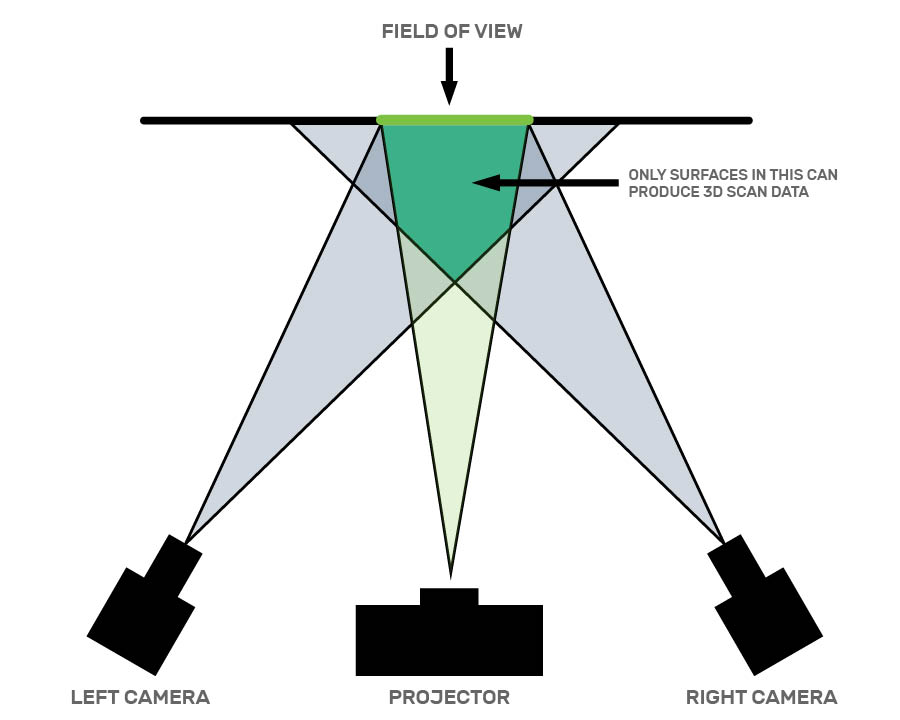
1. Spotlight on Structured Light 3D Scanning
For more on the basics of structured light 3D scanning; see part 1 in our 3D Scanning 101 series Basics of Structured Light
Advantages
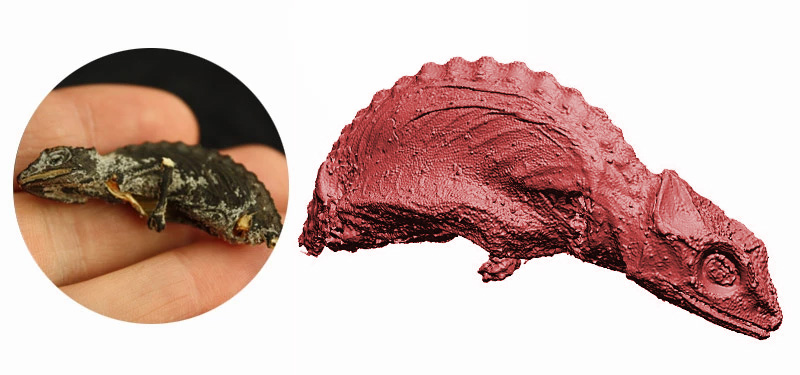
Fine Details: Structured light scanners are champions when it comes to intricate details. This precision makes them a favorite in industries where details are important, such as heritage preservation, jewelry or component manufacturing. Ideal for scanning objects with dark spots and undercuts, which can be time-consuming to process with laser scanning.
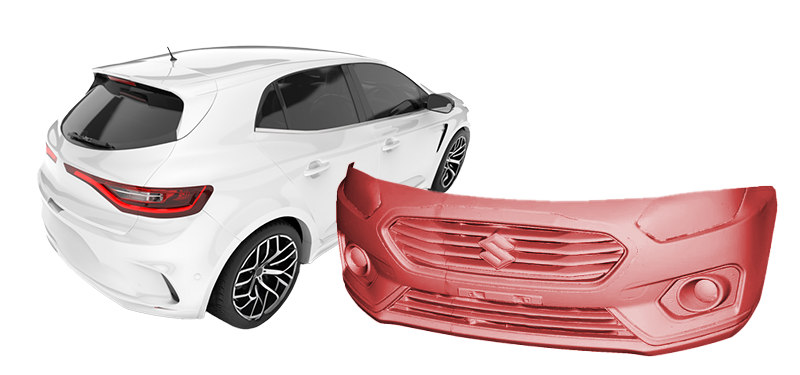
Organic Shapes: Structured light systems can capture thousands of points simultaneously, making them ideal for complex organic shapes such as automotive body panels; scanning significantly faster than laser, which captures data point-by-point. Especially advantageous with large and very large organic shapes.
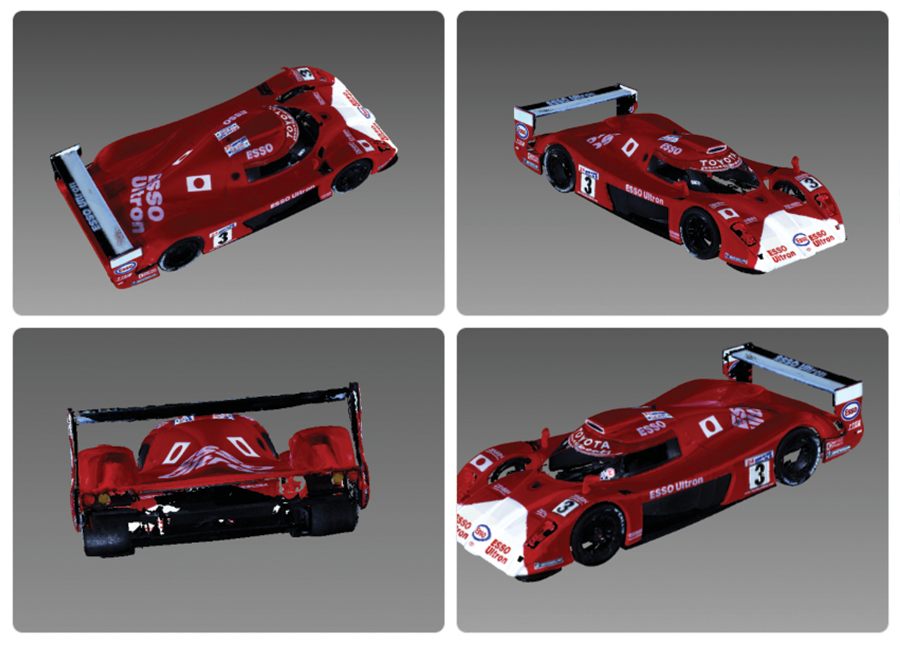
Color & Texture Mapping Capabilities: High-Quality Texture Data is a forte of structured light 3D scanning: These 3D scanners accurately map the color and texture of the object’s surface, a feature often lacking in low to mid range laser scanners.
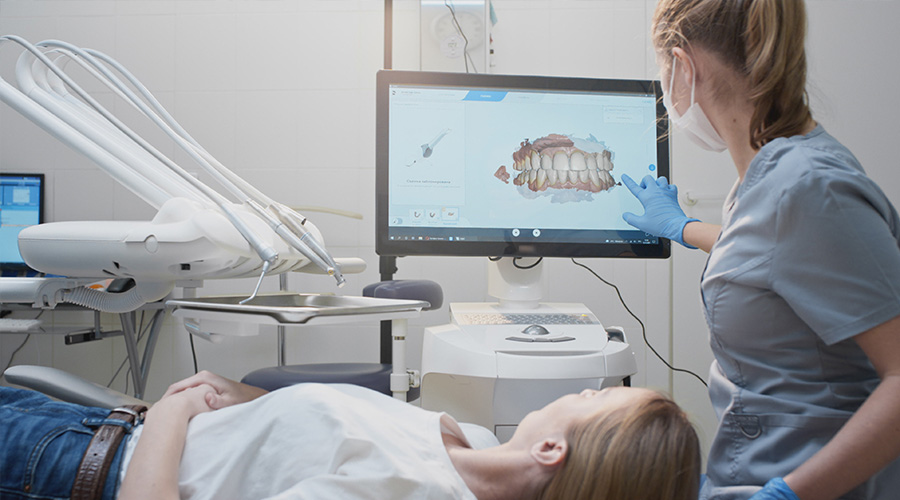
Improved Safety & Comfort: Structured light is a non-Intrusive Technology: The use of harmless light patterns makes structured light scanners safe for scanning biological subjects, including humans, without the discomfort or safety concerns associated with laser exposure.
Adaptable to Lighting Conditions: Structured light scanners are less sensitive to ambient lighting variations compared to laser scanners, making them more versatile in some environmental conditions.
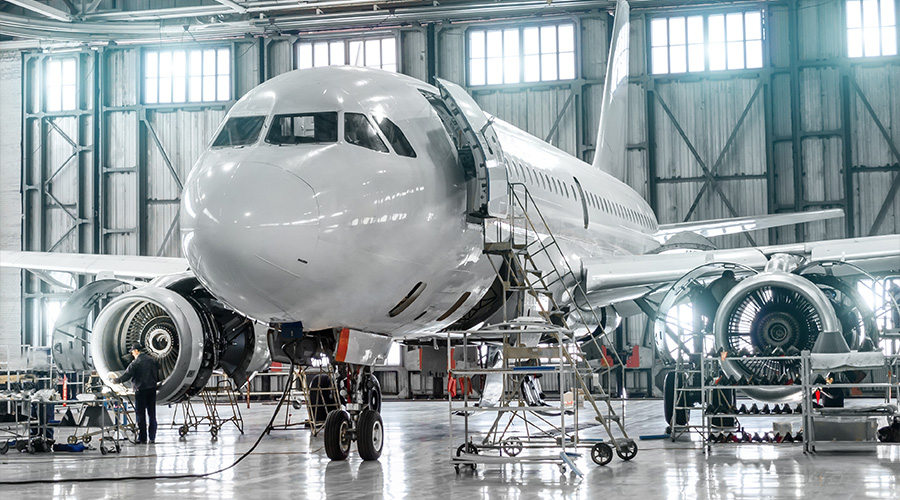
Scalable: Capable of scanning objects of varying sizes, from small industrial components to large architectural structures with the option to stitch scans together to achieve a larger 3D model making them extremely versatile.
User-Friendly: Structured light systems are generally more user-friendly, requiring less technical expertise to operate effectively. These devices tend to be more compact and portable, making them ideal for fieldwork.
Disadvantages
Light Sensitivity: A structured light scanner’s kryptonite is extremely dark or reflective surfaces. This sensitivity can lead to data inaccuracies, making them less ideal for scanning shiny or outdoor objects.
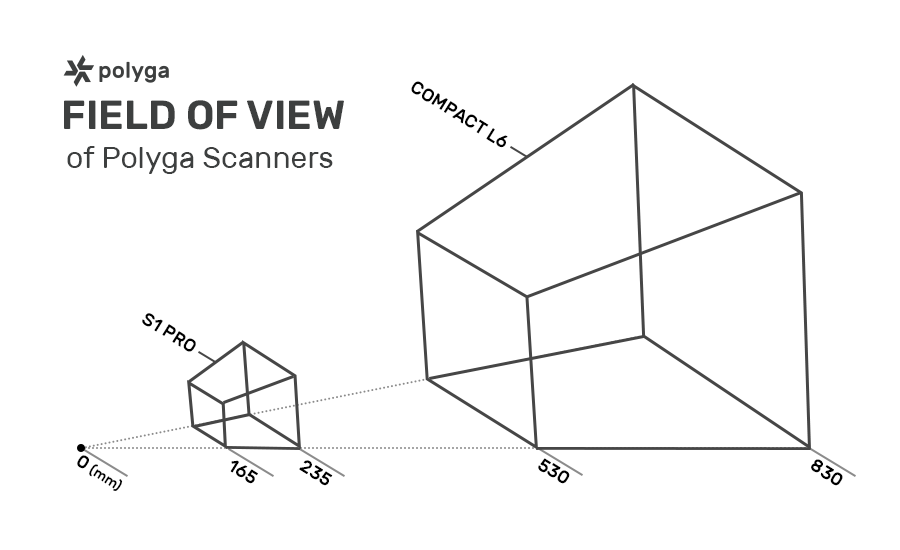
Range Limitations: These scanners are not the best fit for large-scale projects. Their limited range can be a constraint in applications like architecture or large machinery scanning.
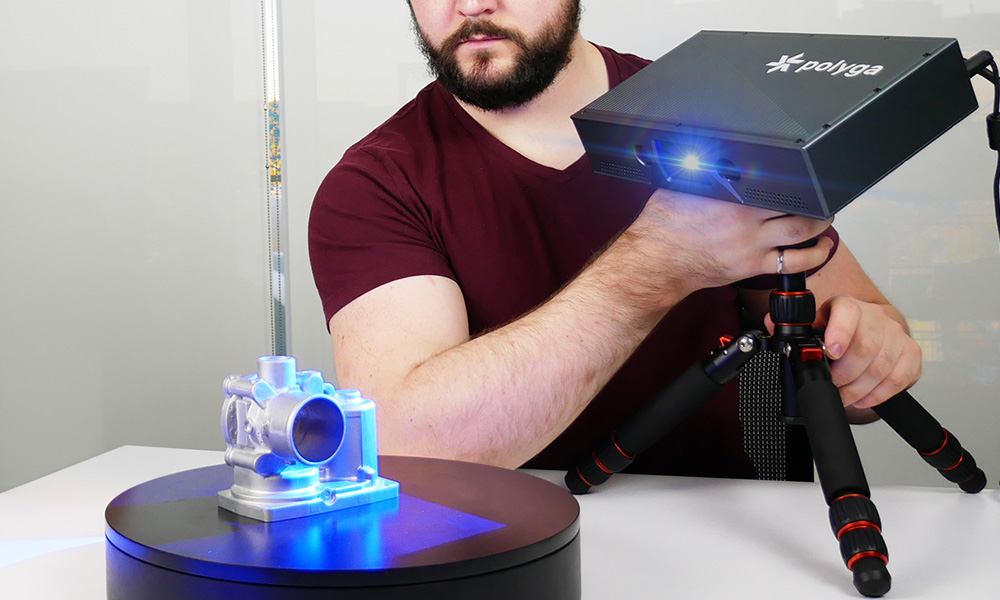
Setup Sensitivity: Getting a structured light scanner ready requires more than just plug-and-play. The setup and calibration require a meticulous approach, which can be challenging for novices.
2. Structured Light Key Takeaway
Structured-light 3D Scanners are great at capturing complex surfaces, especially high detailed organic shapes. These objects are challenging for other measurement devices like calipers, hand gauges, and portable CMMs to take surface measurements due to their rigidity. Imagine the difficulty of taking measurements off an organic freeform object using conventional measurement tools. Structured-light 3D scanners are optical measurement devices that can capture about 1,000,000 3D data points in under 1 second.

3. Shining a Light on Laser 3D Scanning
3D Laser Scanning is a non-contact, non-destructive technology that digitally captures the shape of physical objects using a line of laser light. 3D laser scanners create data from the surface of the object. 3D laser scanners like structured light scanners measure and capture free-form shapes to generate point clouds.
Laser 3D scanning works much like the echolocation used by bats. By emitting a laser beam towards an object, the scanner measures the time it takes for the light to bounce back.
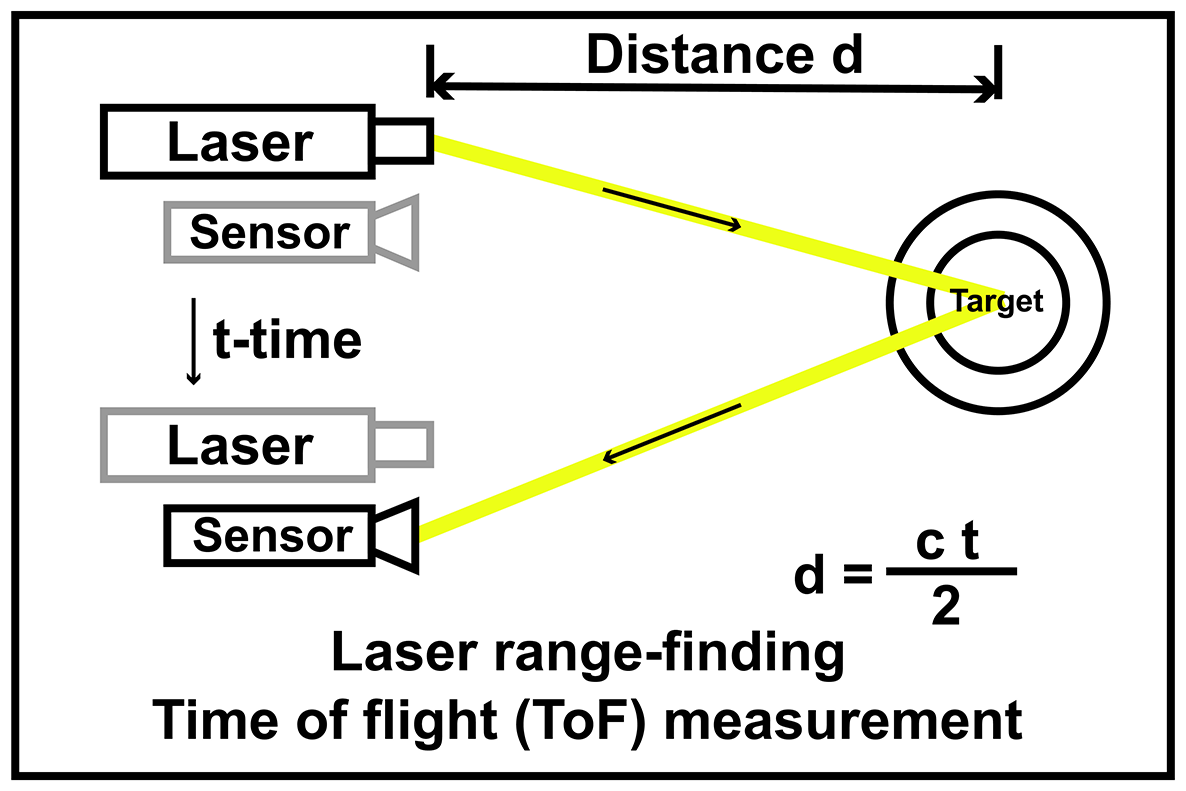
This ‘time of flight’ is then converted into a distance measurement. Just like a painter adds brush strokes to a canvas, the scanner sweeps over the object, collecting distance points.
Laser Advantages
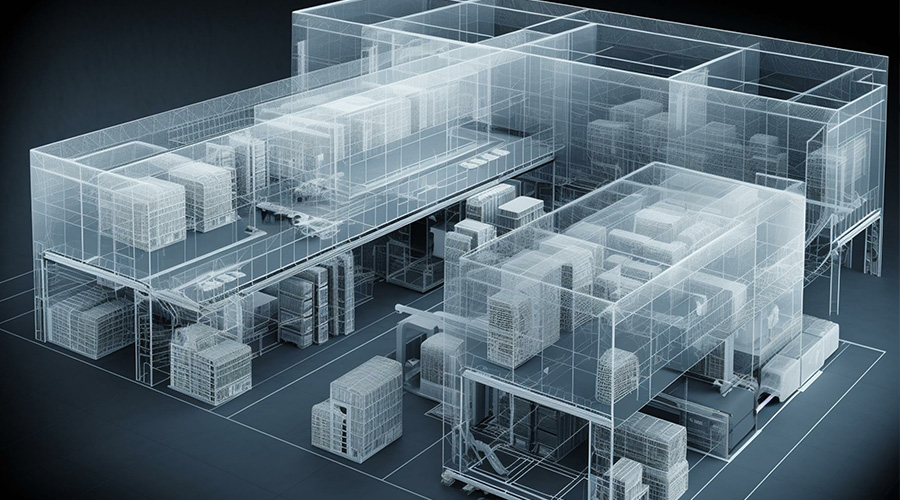
Long-Distance Relationship: Laser scanners excel in capturing objects far and wide. Their ability to scan large objects and areas from a distance makes them indispensable in construction, topography, and large-scale industrial applications.
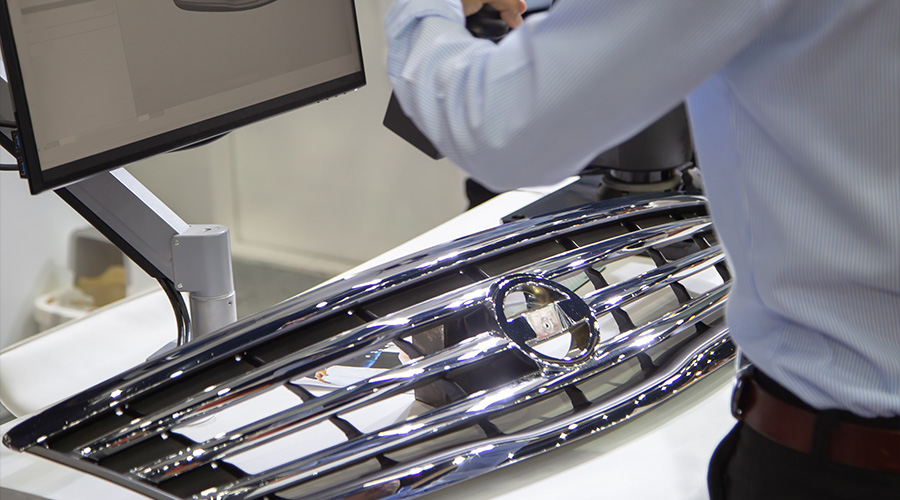
Special Surfaces: Laser scanners are less affected by complex light refraction issues caused by very shiny and very dark objects, the ability to scan very shiny dark surfaces, gives them an edge when working with objects with these specific attributes. Some of these issues can be mitigated or solved using 3D scanning spray such as aseub but in cases where the use of spray isn’t an option laser scanning takes the lead.

Depth Perception: When it comes to depth accuracy, laser scanners take the lead. This feature is important in industries where depth precision is non-negotiable.
Laser Disdvantages
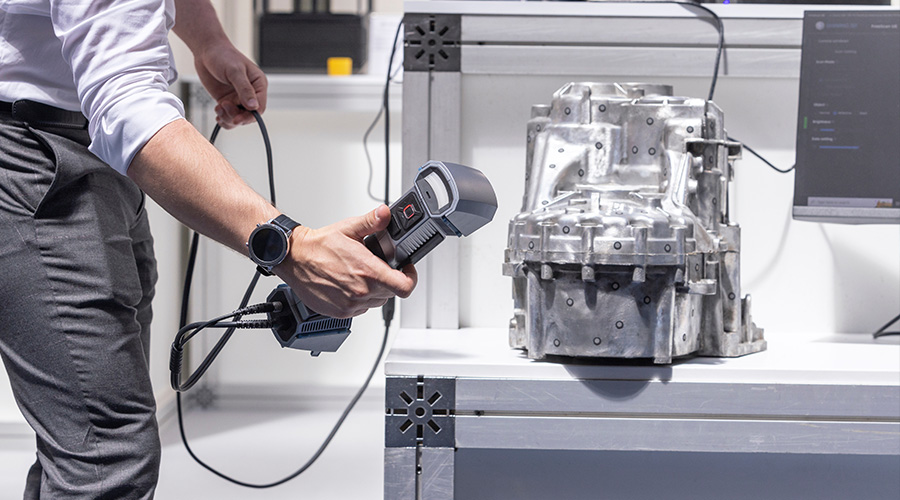
Time-Consuming: Precision takes time, and laser scanners embody this. Their point-by-point data capture method can be slower than structured light scanning, posing a challenge in time-sensitive projects.
Safety: The lasers used, especially in high-precision models, can be hazardous to the eyes, making them unsuitable for scanning living subjects.

Cost & Pricing: Cost & Pricing: Quality comes at a price, and high-grade laser scanners can be a significant investment sometimes costing over $100,000, placing them out of reach for small-scale users or individual enthusiasts.
Color Blind: Capturing color is not a laser scanner’s forte. This limitation can be a drawback in fields where color data is crucial, like digital media or art restoration.
4. Laser Key Takeaway
A major advantage of laser scanning lies in its ability to capture depth as well as vast environments, a feature where structured light scanners typically face limitations due to their field of view constraints. This makes laser scanning the preferred choice for projects like topographical surveys or full-scale architectural modeling. Additionally, laser scanners excel in depth accuracy and applications with very dark or very shiny surfaces.
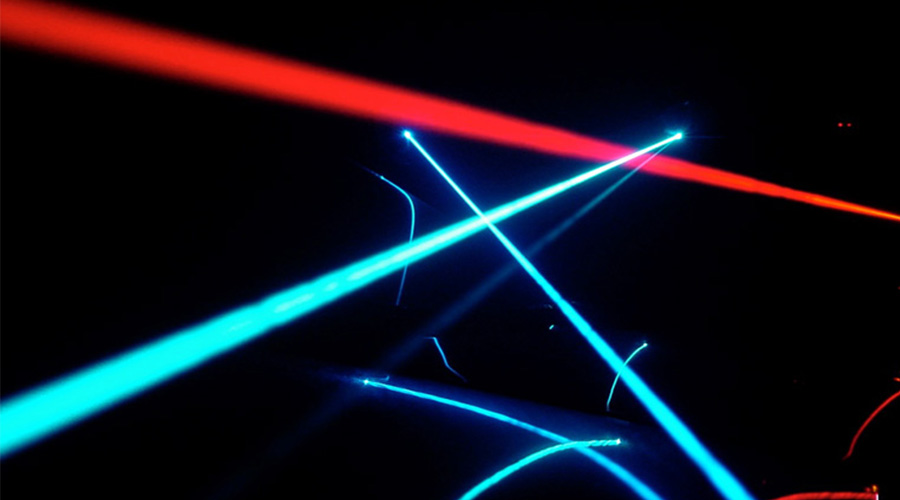
5. Conclusion
The choice between structured light and laser 3D scanning is highly dependent on your specific needs. Structured light scanning is your ally in detail and color-rich projects in controlled environments. Structured Light 3D Scanning stands out for its speed, accuracy, versatility, and user-friendliness. Its capabilities make it a preferred choice in many industries, from industrial design to cultural preservation and beyond.
In contrast, laser scanning stands tall in large-scale, very dark, or very shiny applications. Stay tuned for the next part of our part 5 of “3D Scanning 101” series, where we’ll examine the advantages and disadvantages of structured light and lidar.
In contrast, laser scanning stands tall in large-scale, very dark, or very shiny applications. Stay tuned for the next part of our part 5 of “3D Scanning 101” series, where we’ll examine the advantages and disadvantages of structured light and lidar.
For more insights into structured light 3D scanning, visit Polyga’s 3D Scanning Learning Center.
Further Reading
- Part 1 – 3D Scanning 101: Basics of Structured Light
- Part 2 – 3D Scanning 101: Real World Applications of Structured Light
- Part 3 – 3D Scanning 101: Size Limitations of Structured Light
- Part 4 – 3D Scanning 101: Structured Light VS LASER
- Part 5 – 3D Scanning 101: Structured Light VS LiDAR
I hope that this article is helpful to you on your 3D scanning journey.
And, if you have any other questions about what type of scanner is right for your project,
feel free to send them to our sales team at sales@polyga.com, and they will be happy to help.
Best regards,
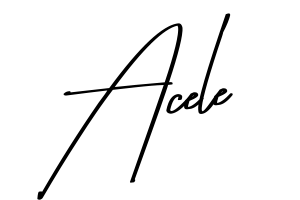
Ace Le
Polyga Inc.
Vancouver, British Columbia, Canada
Email: contact@polyga.com
Website: Polyga.com