Precision, efficiency, and innovation are the pillars of modern engineering and manufacturing. And 3D scanning reverse engineering is rapidly becoming indispensable in achieving these goals. This technology transforms industries and empowers professionals to create, replicate, and optimize products with unprecedented accuracy.
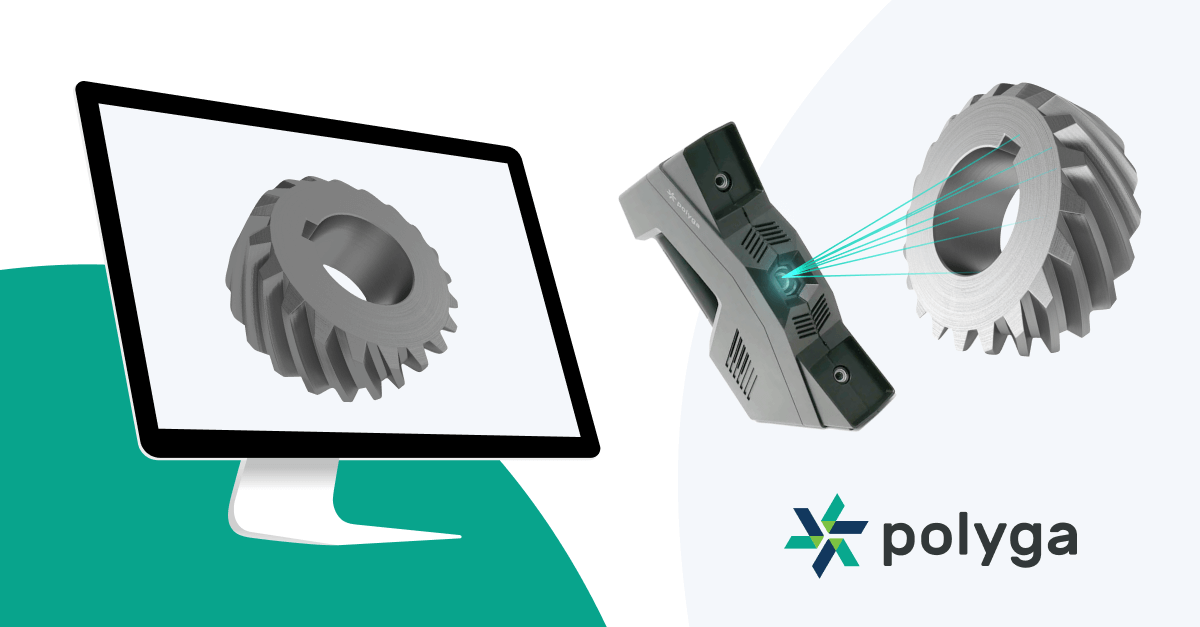
Fundamentals of 3D Scanning for Reverse Engineering
Beyond visuals, 3D scanning provides a comprehensive understanding of the object’s physical properties. This technology is transforming industries that prioritize precision and efficiency.
3D Scanning Technologies Types
There are three main types of 3D scanning technologies, each suited for specific applications:
Laser Scanning: Uses laser beams to measure distances and capture surface details. Ideal for industrial applications requiring high precision.
Photogrammetry: Uses multiple photographs to create 3D models. Suitable for large objects where extreme accuracy isn’t the top priority.
Structured Light Scanning: Projects complex light patterns onto objects, capturing even the smallest details with exceptional precision. Ideal for high-accuracy tasks like healthcare.
Technology | Description | Suitable For |
Laser Scanning | Uses laser beams to measure distances and capture surface details. |
High-precision tasks. |
Photogrammetry | Uses photographs to create 3D models. |
Large objects, less precision required. |
Structured Light | Projects light patterns to measure deformations and capture details. |
Detailed, high-accuracy applications. |
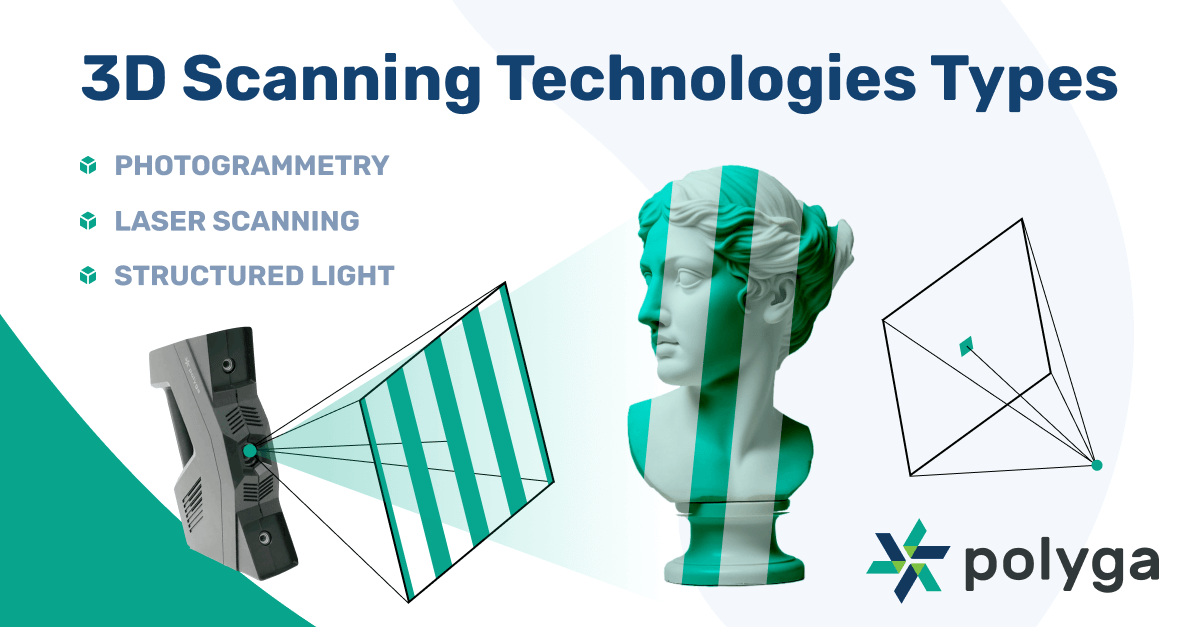
3D Scanner Key Components
A 3D scanner is a sophisticated device composed of several essential components that work together to capture accurate digital representations of physical objects. The main parts include sensors, cameras, and processing software. Here’s an overview of each component and its role.
Sensors: Sensors are critical for detecting the light patterns projected onto the object. They measure the distance between the scanner and the object’s surface, ensuring precise data collection.
Cameras: Cameras capture the deformation of light patterns on the object’s surface, translating these visual cues into digital information. High-resolution cameras are essential for capturing fine details and intricate features.
Processing Software: After capturing the data, the processing software diligently converts it into a usable digital format, like a dense triangle mesh or point cloud, ensuring its accessibility. This software is crucial for data refinement, noise reduction, and creating accurate 3D models ready for reverse engineering.
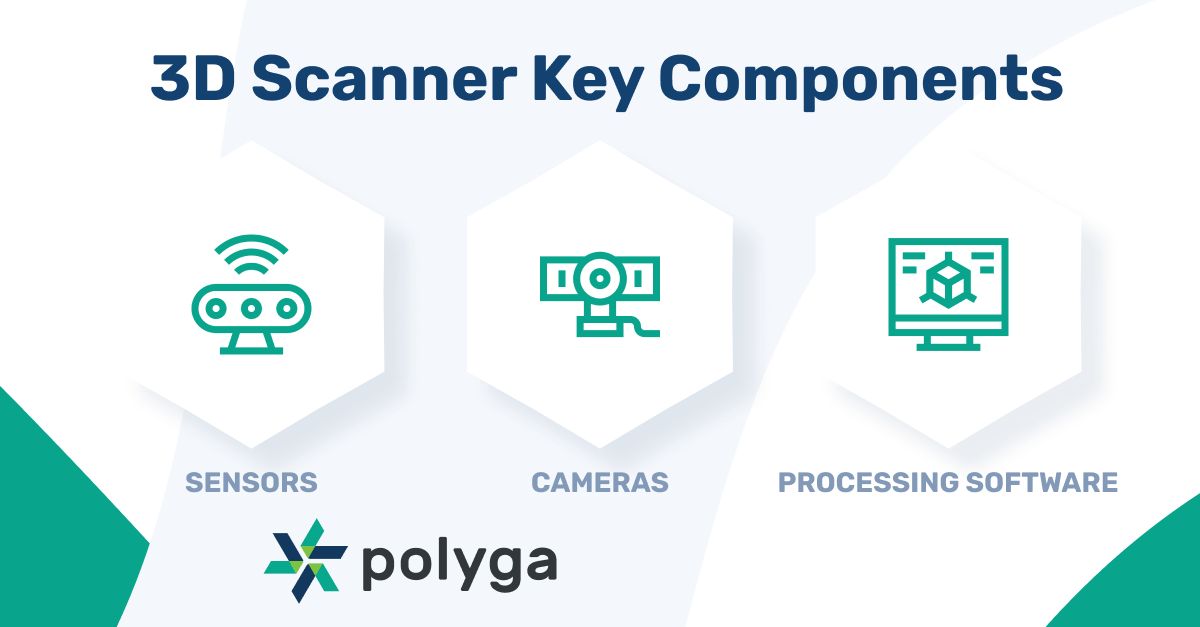
Guide to Reverse Engineering
Reverse engineering is deconstructing a physical object to understand its design and function. Think of it as “working backward” from the finished product. 3D scanning revolutionizes reverse engineering by providing a digital blueprint of the object, making it easier to analyze, modify, and recreate.
3 Essential Steps
The typical reverse engineering process involves three key stages:
- Data Capture: The 3D scanner meticulously collects the object’s surface data, creating a point cloud that represents its shape.
- Data Processing: Specialized software converts the raw scan data into a usable 3D model, typically in formats like OBJ, PLY, or STL.
- CAD Model Creation: CAD software, such as SOLIDWORKS, in combination with Polyga’s XTract3D add-on, enables engineers to create a parametric model that is easily editable and optimized.
Reverse Engineering: Software and Tools
Several software tools are essential for processing 3D scan data and aiding in reverse engineering. These tools offer various features that streamline the workflow and enhance the accuracy of the final digital models.
SOLIDWORKS: Widely used CAD software with robust tools for creating precise 3D models. It allows engineers to import 3D scan data for building parametric models, offering tools for sketching, modeling, and validating designs.
XTract3D: An add-in for SOLIDWORKS designed for reverse engineering. It provides slicing, fitting, and snapping tools to trace 3D scan data directly within SOLIDWORKS, simplifying the creation of accurate digital models.
There are dozens of other software tools. Geomagic Design X integrates with CAD applications like SOLIDWORKS and Autodesk Inventor, offering surfacing, mesh editing, and parametric model creation tools. Autodesk ReCap processes 3D scan data, converting point clouds and meshes into detailed models, and integrates with Autodesk’s design software, such as AutoCAD and Fusion 360. MeshLab is an open-source tool for cleaning, filtering, and converting 3D triangular meshes. PolyWorks is an in-depth metrology suite that aligns and compares scanned data with CAD models, making it ideal for inspection and quality control.
Applications of 3D Scanning in Reverse Engineering
3D scanning reverse engineering revolutionizes industries by enhancing part replication, improvement, and customization. In automotive, it captures the dimensions of discontinued parts for better performance and reduced costs. In aerospace, it ensures precise inspection and maintenance. For consumer products, it speeds up design modifications and time-to-market. Let’s review deeper.
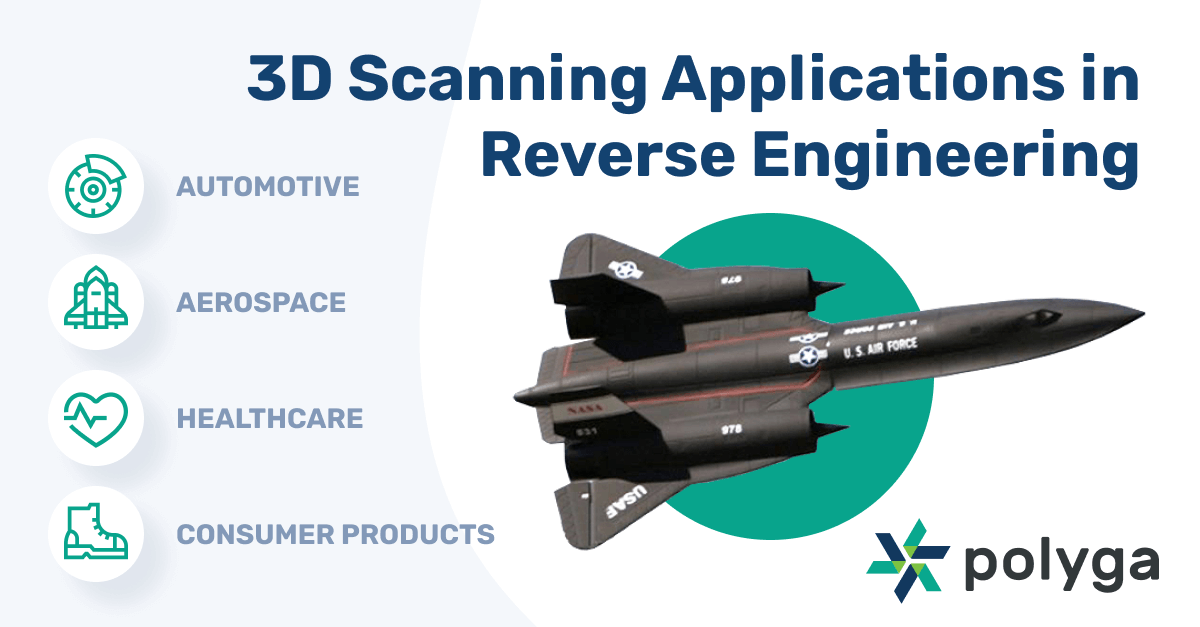
Industrial Applications
3D scanning has revolutionized various industries by enhancing reverse engineering capabilities.
Automotive: 3D scanning quickly replicates and improves parts. It captures the exact dimensions of discontinued parts, enabling engineers to create CAD models for better performance and easier manufacturing, reducing prototyping time and costs.
Aerospace: 3D scanning precisely inspects and reverse engineers complex components like turbine blades and fuselages, ensuring safety and performance. It aids in developing replacement parts and maintaining older aircraft by creating accurate digital models of legacy parts.
Consumer Products: 3D scanning facilitates redesign and customization. Companies scan products, analyze designs, and modify them to enhance functionality and aesthetics, speeding up time to market and ensuring high quality in industries like consumer electronics.
Case Studies
3DRE 3D Scanning Services Ltd.: Matthew Percival used the Polyga Compact S1 scanner and XTract3D software to reverse engineer a small mechanical assembly. The specialist used a scanning spray on the reflective surfaces to improve detail capture. Data processed in SOLIDWORKS using XTract3D ensured precise parametric model creation. Re-scanning and comparing the manufactured part with the original model resolved fit issues, demonstrating effective quality control.
Cultural Heritage Preservation: Polyga’s 3D scanner was used to create digital replicas of historical artifacts. This preserved their physical features and allowed for further study and virtual interaction without risking damage. The digital models captured intricate details, providing valuable resources for researchers and educators.
These reverse engineering examples highlight the transformative impact of 3D scanning on product development and troubleshooting. Advanced 3D scanning reverse engineering technologies enhance accuracy, efficiency, and innovation across industries.
Challenges and Limitations
3D scanning reverse engineering faces challenges in achieving high accuracy and resolution, as lower resolution can miss features and cause errors in CAD models. Material and surface finishes also affect scan quality, requiring specific techniques and tools for precise data capture.
Accuracy and Resolution Issues
High accuracy and resolution are challenging to achieve. Lower resolution can miss critical features, leading to CAD model inaccuracies. Using high-quality scanners like Polyga’s and regular calibration can mitigate these issues.
Material and Surface Challenges
Material properties and surface finishes impact scan quality. Reflective, transparent, or dark surfaces can cause data capture issues. Using scanning sprays, markers, and structured light scanning can improve accuracy. Understanding these factors is crucial for high-quality scans.
Future Trends and Innovations in 3D Scanning for Reverse Engineering
Technological advancements are making 3D scanning reverse engineering faster and more precise. Miniaturized scanners and real-time data processing streamline workflows, while portable devices enable on-site scanning.
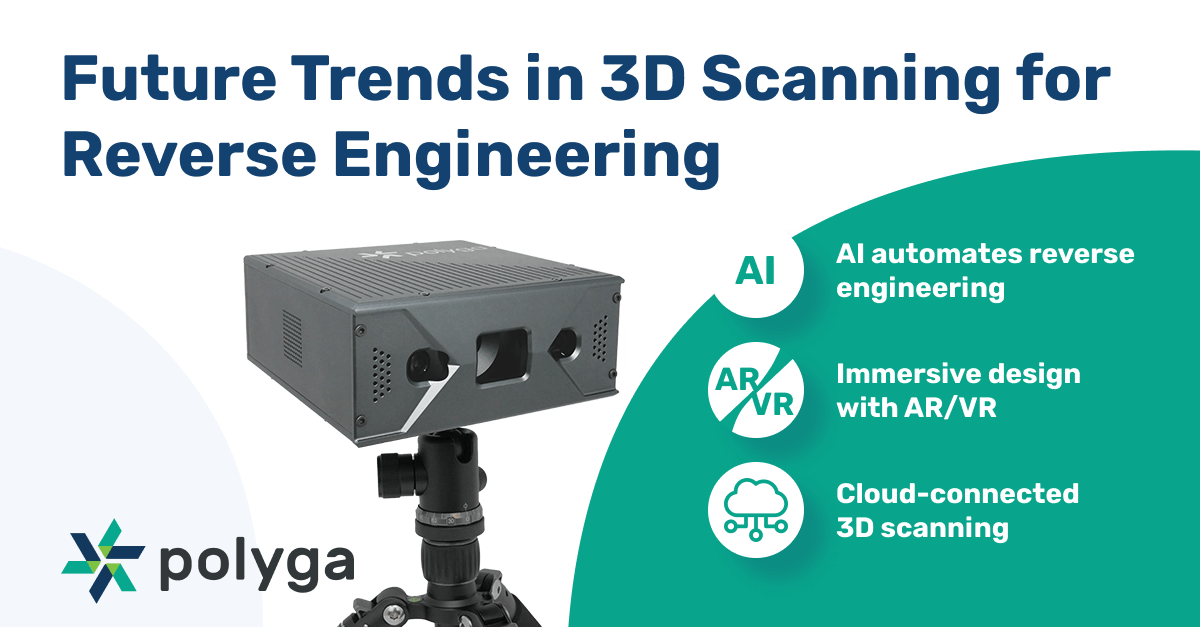
Advancements in Technology
New scanners are becoming faster, more accurate, and capable of capturing finer details. Miniaturized devices allow the scanning of smaller parts, while real-time data processing provides immediate feedback, reducing post-processing time.
Integration with Other Technologies
Integrating 3D scanning with AI and AR/VR revolutionizes reverse engineering. AI automates data capture and processing, optimizing scan settings and creating CAD models. AR/VR enables immersive interaction with scan data, enhancing collaborative design and validation processes.
How To Choose The Proper 3D Scanner For Reverse Engineering
Selecting the right 3D scanner for reverse engineering requires understanding your project’s needs and considering key factors. Start by identifying the primary application, whether it’s aerospace, manufacturing, medicine, or architecture, as each has unique requirements.
Crucial factors include the scanner’s durability, image quality, and accuracy. Look for robust materials and advanced imaging systems, like dual 5MP cameras and blue light projectors, to enhance data fidelity. Also, consider automation capabilities to future-proof your investment. By evaluating these aspects, engineers can choose a scanner that supports efficient, precise reverse engineering workflows.
Implement 3D Scanning for Reverse Engineering Projects
3D scanning reverse engineering revolutionizes industries, from replicating car parts to preserving artifacts. We’ve covered the fundamentals, processes, and tools, highlighting impacts on automotive, aerospace, and consumer products. Technological advancements and AI/AR integration promise a bright future despite challenges.
Ready to harness this power?
Contact us today to unlock the full potential of 3D scanning for your reverse engineering needs.
FAQ
Q1: Which step in the reverse-engineering process involves the redesign and optimization of the product?
The redesign and optimization occur during the CAD model creation phase. After capturing and processing the scan data, engineers use CAD software to refine the model, apply improvements, and ensure the new design meets the desired specifications and performance criteria.
Q2: What data is important to collect during the reverse engineering process?
During reverse engineering, it is crucial to collect accurate geometric measurements, surface details, and material properties of the object. This data guarantees that the digital model is accurate and can efficiently reproduce, alter, or enhance the original design.