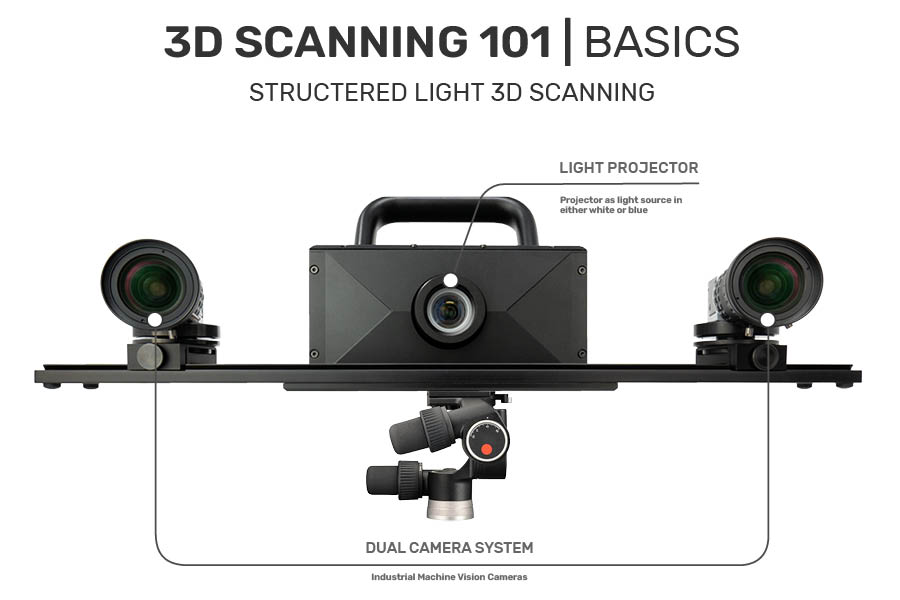
3D Scanning 101 Part 1
The Basics of Structured Light 3D Scanning
1.0 Introduction
What makes Structured Light the go-to method for 3D scanning? How does it work? Why should it matter?
Whether you’re new to structured light 3D scanning or a seasoned pro looking for a refresher, this multi-part series dives into a comprehensive look into what makes this technology trusted across various industries for its precision, versatility, and efficiency.
Contents
- 1.0 Introduction
- 1.1 What is Structured Light 3D Scanning?
- 1.2 Principles of Structured Light 3D Scanning
- 1.3 Limitations
- 2.0 Basics of Scanning With Structured Light
- 2.1 Projection
- 2.2 Capture
- 2.3 Processing and Analysis
- 2.4 Creating the 3D Model
- 3.0 Advantages of Structured Light
- 3.1 High-Accuracy and Resolution
- 3.2 Light Sensitivity
- 3.3 Speed and Efficiency
- 3.4 Non-Invasive and Safe
- 3.5 Conclusion
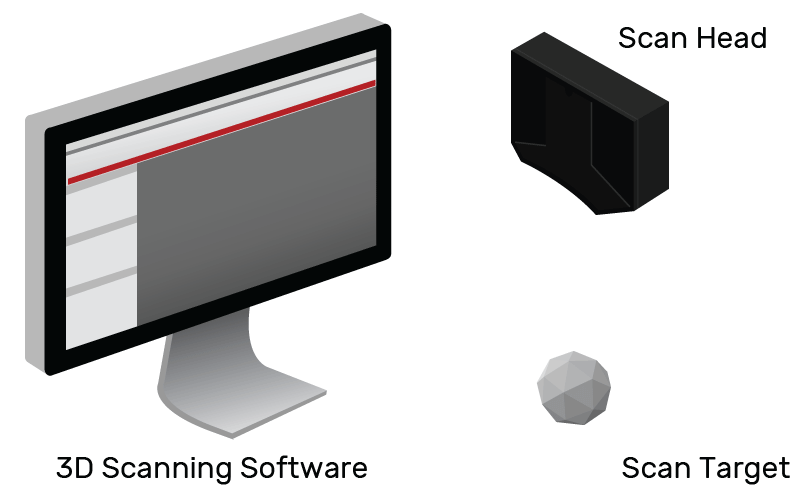
1.1 What is Structured Light 3D Scanning?
Structured light 3D Scanning might sound like a complex term, but put simply, it’s a non-contact optical 3D scanning method used to capture shapes and dimensions of objects by projecting light patterns onto a surface. These patterns deform upon the object, and the distortion is captured by a camera system. The data is then collected and processed to construct a digital 3D model.
1.2 Principles of Structured Light 3D Scanning
The core principle of structured light 3D scanning revolves around triangulation. By projecting a known pattern onto an object and capturing it from different angles, the system can calculate the depth and surface contours of the object with high precision.
Triangulation uses the geometric principle where the location of a point in space is determined by forming a triangle to that point from known positions. In practical terms, a 3D scanner projects a laser or patterned light onto the subject. At the same time, one or more cameras, positioned at a distance from the projector, capture the light as it bounces off the object’s surface. This data is then used to reconstruct a 3D model of the object.
1.3 Limitations
The accuracy of triangulation-based 3D scanning is highly dependent on the precision of the projected light or laser, the quality of the camera sensors, and the calibration between the camera and projector. Widely adopted for its accuracy and effectiveness in capturing fine details, making it an essential tool in applications requiring high-accuracy and high-precision.
2.0 Basics of Scanning With Structured Light
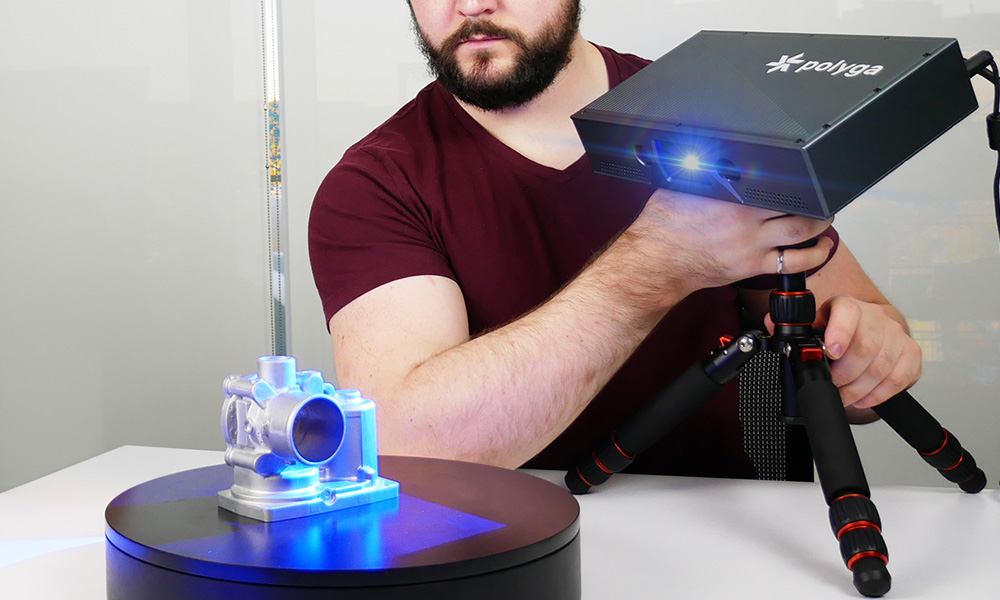
2.1 Projection
The first step involves projecting a light pattern onto the object. The nature of the pattern can vary, but it’s essential for the system to recognize and analyze the deformations accurately.
2.2 Capture
Multiple cameras, strategically placed, capture the distorted pattern. This step is crucial as the accuracy of the final 3D model hinges on the quality of these captured images.
2.3 Processing and Analysis
Specialized software processes the captured images. It compares the deformed pattern to the original and calculates the 3D coordinates of each point on the object’s surface.
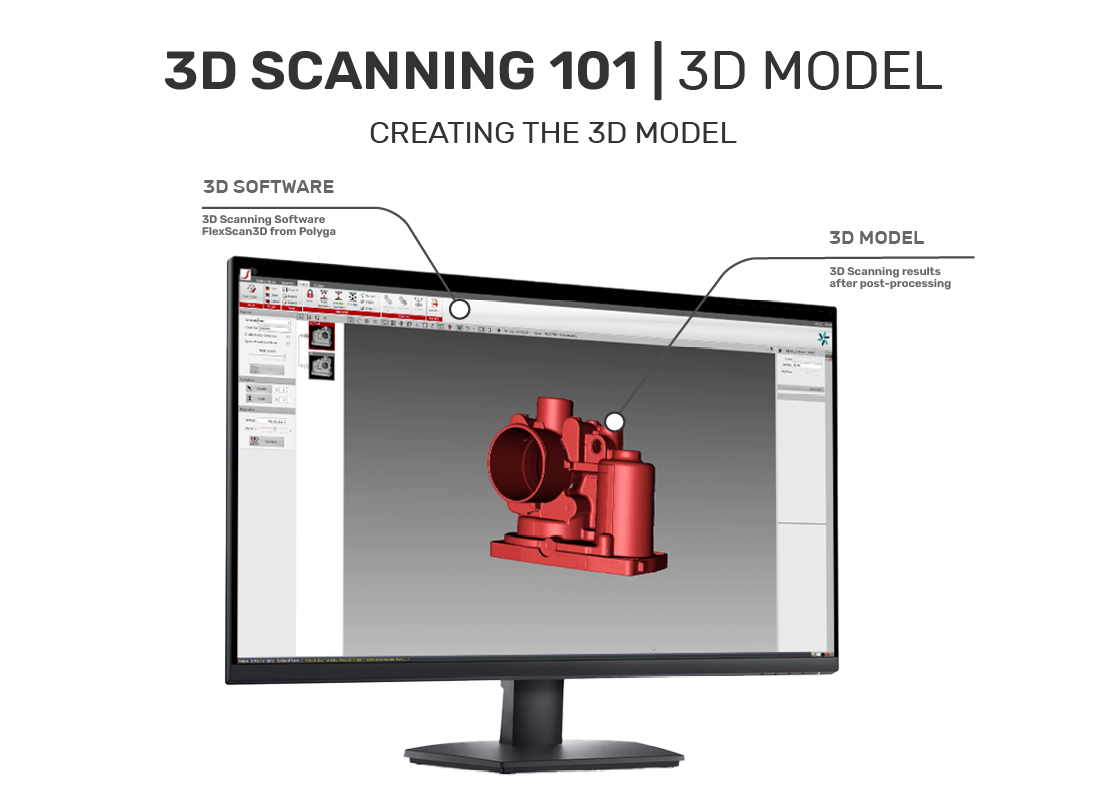
2.4 Creating the 3D Model
Finally, the software compiles the data points to create a digital 3D representation of the object. This model can be used in various applications, from manufacturing to virtual reality.
3.0 Advantages of Structured Light
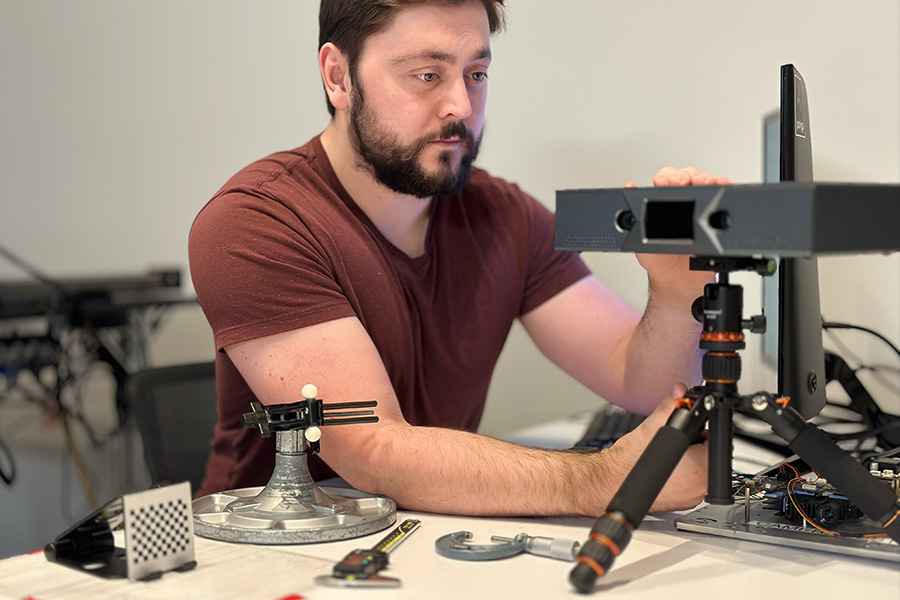
3.1 High-Accuracy and Resolution
Structured light 3D scanning is often hailed as one of the most accurate and high-resolution methods currently available, a distinction it earns due to several key attributes:
- This method employs a sophisticated interplay of light projection and camera capture to precisely measure an object’s surface.
- The accuracy comes from the scanner’s ability to project finely detailed and complex light patterns.
- Structured light provides the highest spectrum of colors and shapes, capturing fine details and subtle surface textures that might elude less sensitive scanning methods like lidar and laser.
- These patterns create rich datasets that, when captured by high-resolution cameras, provide an extremely detailed map of the surface.
Additionally, structured light scanners often employ multiple cameras, allowing for multiple perspectives of the light patterns. This multi-camera approach improves overall accuracy by minimizing shadows and occlusion dropout errors, or “blind spots”, but also contributes to better positioning triangulation and 3D models.
3.2 Light Sensitivity
Structured light scanners are less sensitive to external lighting conditions compared to other scanning technologies such as lidar or laser.This helps maintain consistent accuracy across various environmental conditions. The controllability of structured light patterns allow for repeatable, reliable measurements. This makes structured light the superior choice for applications requiring the best in accuracy and resolution.
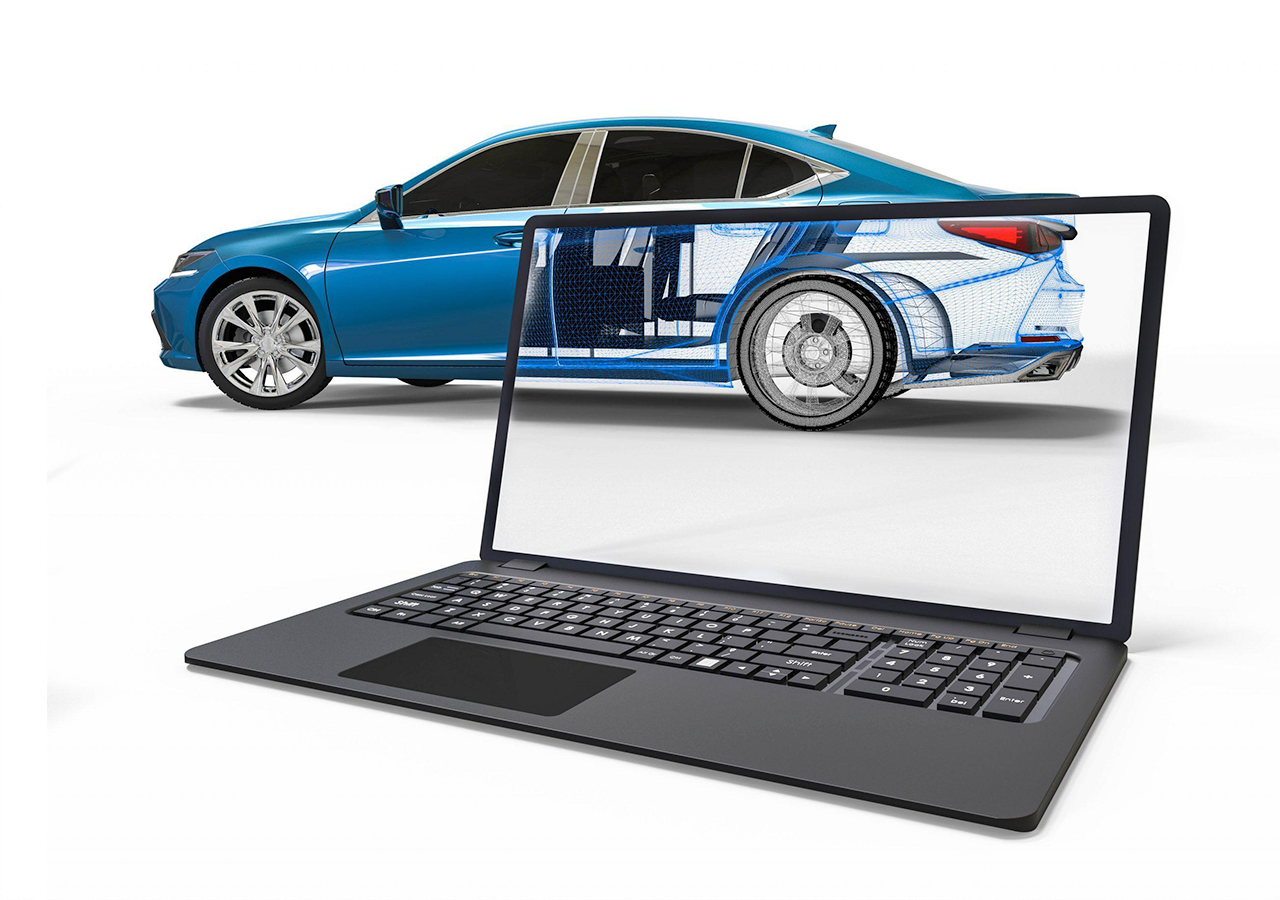
3.3 Speed and Efficiency
Structured light 3D scanning is renowned for its speed, outpacing many other scanning methods, largely due to its ability to project patterns and capture large amounts of data in a single pass. Unlike point-based techniques like laser scanning, which typically collect a single data point at a time, structured light scanners project a pattern across the surface of the object allowing the scanner to process much larger data-sets.
This speed advantage is further expanded on by processing software that can quickly interpret these data-sets to create a 3D model. Capturing large data-sets reduces the need for multiple passes, significantly speeding up the overall scanning process. This is especially valuable in industries where speed is a critical factor, as in quality control or human scanning.

3.4 Non-Invasive and Safe
As a non-contact method, structured light is safe for delicate objects and can be used without risk to the operator or the subject.
This stems from the technology’s use of light rather than physical contact or potentially harmful radiation, as found in some other scanning methods. Since there is no need for direct contact, the risk of damaging delicate or fragile objects, such as historical artifacts, artworks, or biological specimens, is minimized.
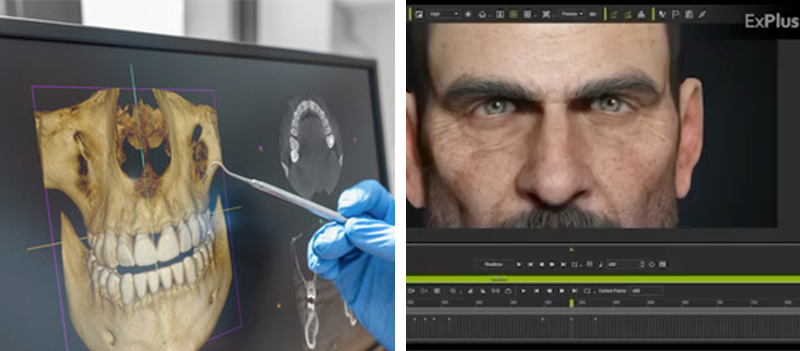
This is a critical consideration in human scanning applications like medical or special effects in film or television. These factors make structured light 3D scanning a go-to for applications where preserving the condition of the object and ensuring the safety and comfort of individuals are needed.
3.5 Conclusion
Structured light 3D scanning is more than a technology; it’s a gateway. It blends accuracy, speed, and versatility to make it the optimum choice in so many different applications. As structured light continues to evolve, its applications are only set to expand, solidifying its role as a staple in modern digital workflows.
From industrial design and quality control to cultural heritage preservation and healthcare. Learn more in our next 3D Scanning 101: Applications for Structured Light Scanning.
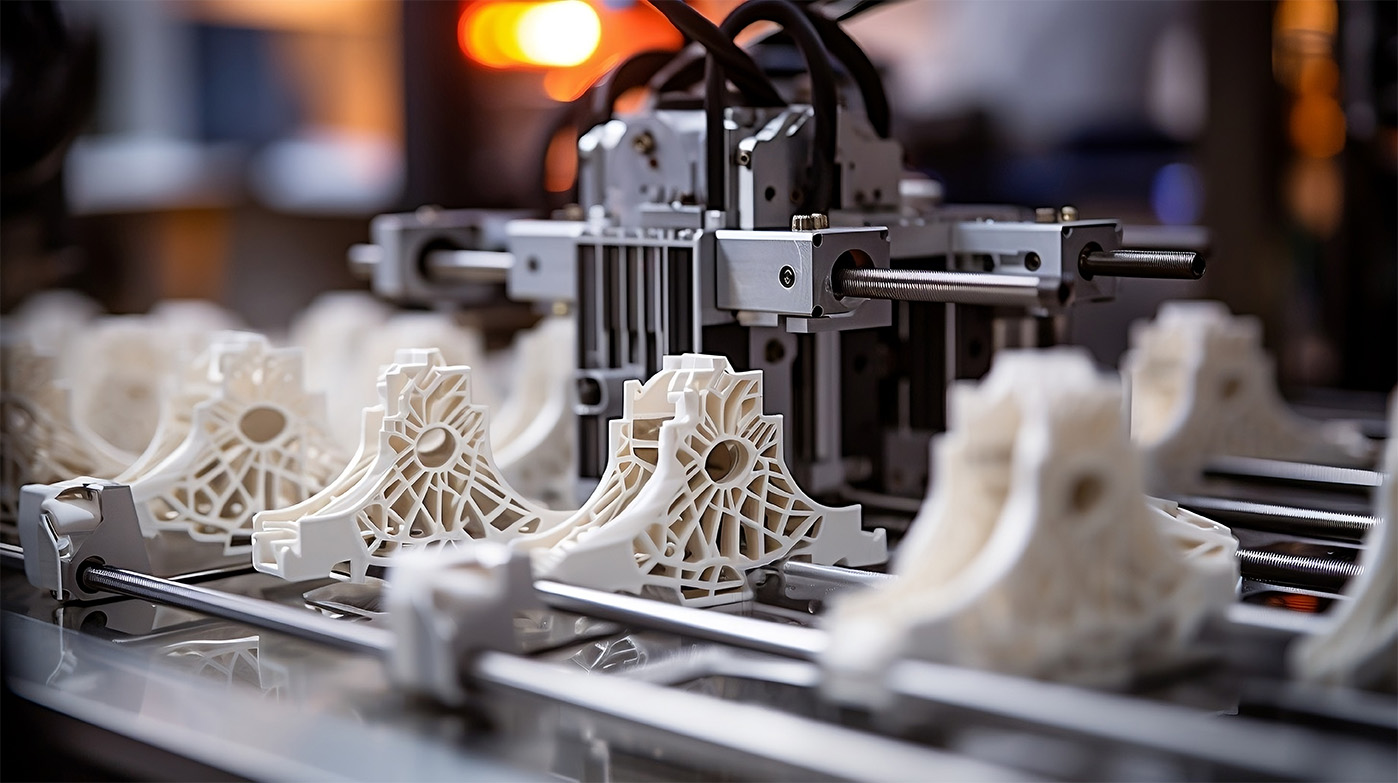
Polyga’s Structured Light 3D Scanners
Polyga offers a range of cost-effective industrial structured light 3D Scanners, catering to the diverse needs of professionals and leaders. From Compact series to the Pro series, versatile models for small macro scanning to advanced configurable systems designed for larger and more complex applications, Polyga’s scanners are at the forefront of 3D scanning technology.
For further exploration into structured light 3D scanning technologies visit our 3D Scanning Learning Center.
Further Reading
- Part 1 – 3D Scanning 101: Basics of Structured Light
- Part 2 – 3D Scanning 101: Real World Applications of Structured Light
- Part 3 – 3D Scanning 101: Size Limitations of Structured Light
- Part 4 – 3D Scanning 101: Structured Light VS LASER
- Part 5 – 3D Scanning 101: Structured Light VS LiDAR
I hope that this article is helpful to you on your 3D scanning journey.
And, if you have any other questions about what type of scanner is right for your project,
feel free to send them to our sales team at sales@polyga.com, and they will be happy to help.
Best regards,
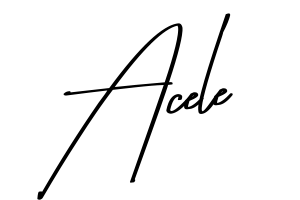
Ace Le
Polyga Inc.
Vancouver, British Columbia, Canada
Email: contact@polyga.com
Website: Polyga.com