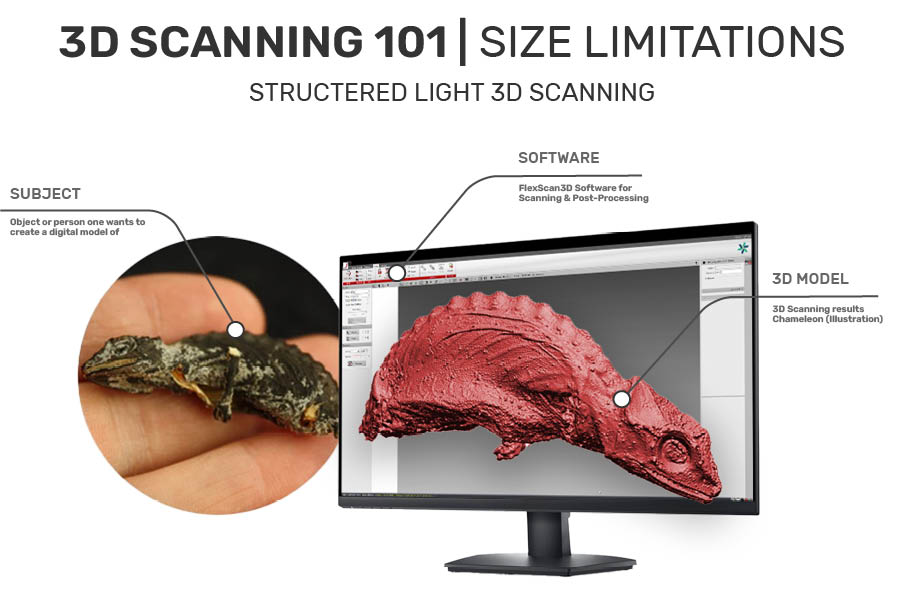
Part 3: Size Limitations of Structured Light 3D Scanning
Introduction
3D scanning has changed the way we capture the physical world in digital form. Structured light technology, which uses projected light patterns and a camera system to measure the three-dimensional shape of objects, is praised for its accuracy and speed. However, like any technology, it has its limitations, particularly regarding the size of objects it can effectively scan.
The limitations of triangulation-based structured light 3D scanning are highly dependent on the precision of the projected light, the quality of the camera sensors, and the calibration between the camera and projector in relation to the size of the object.
Part 3 of our 3D Scanning 101 series delves into the nuances of these size limitations, providing insight into how they affect scanning quality and what users can do to mitigate these challenges.
Contents
- Introduction
- The Fundamentals of Structured Light Revisited
- Balancing Field of View and Resolution
- Limitations
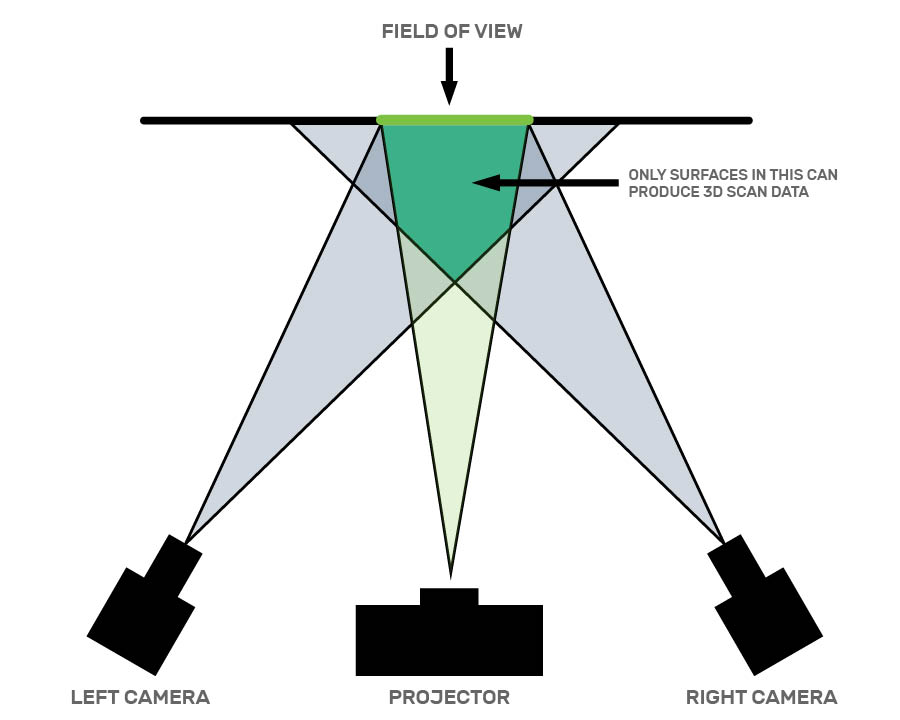
2: The Fundamentals of Structured Light Revisited:
Before discussing size limitations, it’s important to understand the basics of structured light 3D scanning. This method involves projecting a series of light patterns onto an object. The way these lines deform when striking surfaces allows a camera, positioned at a known angle to the projector, to calculate the depth and surface contours of the object. The scanner then compiles these data points to create a detailed 3D model.
Read more in part 1 of our ongoing series 3D Scanning 101: Part 1 of 3D Scanning 101 Basics of Structured Light
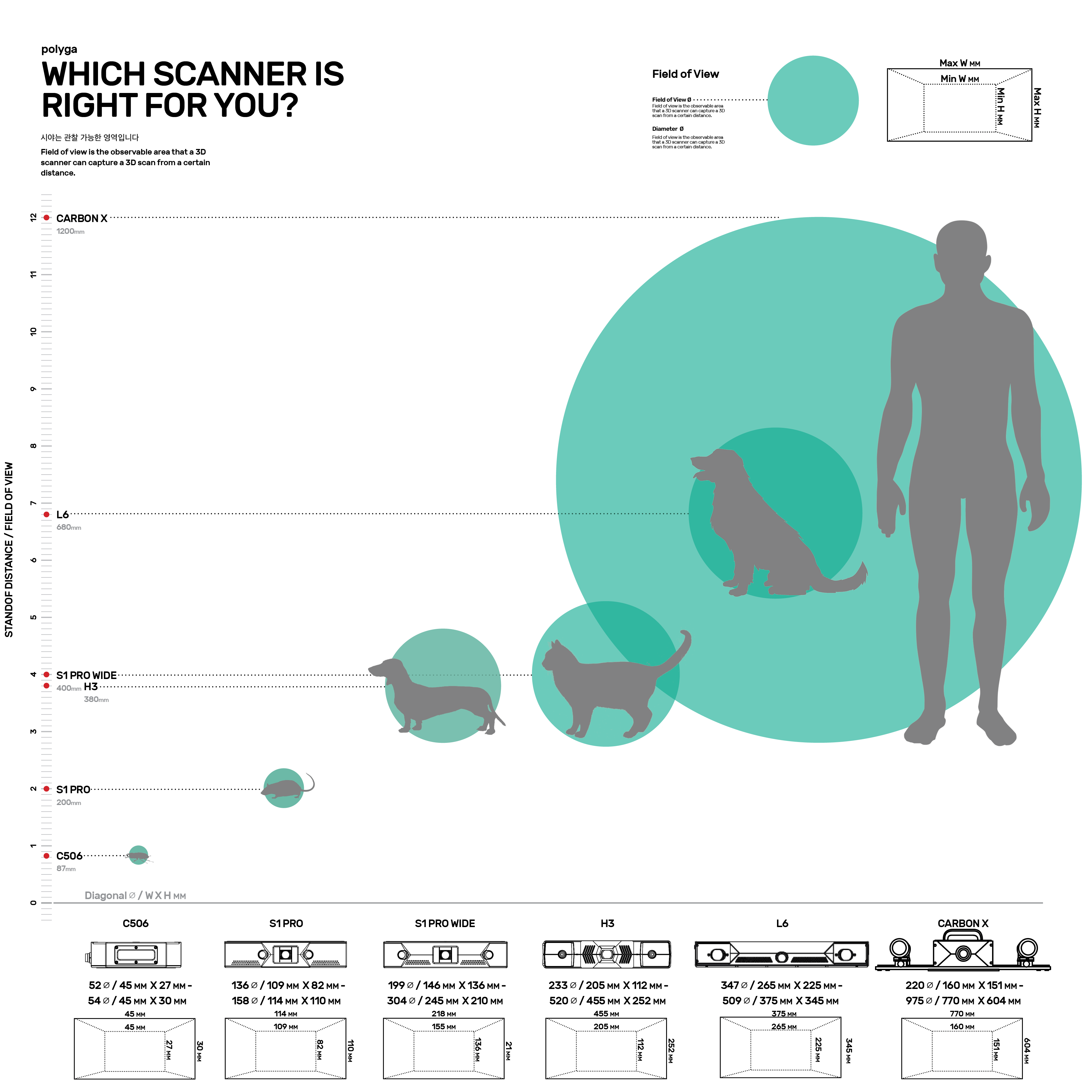
Download PDF
Size Limitations: The Bigger Picture
The primary limitation in structured light scanning relates to the field of view (FOV), the size of the area that the scanner can capture in a single shot. Scanners are typically optimized for specific size ranges, and objects that fall outside these ranges can pose challenge.
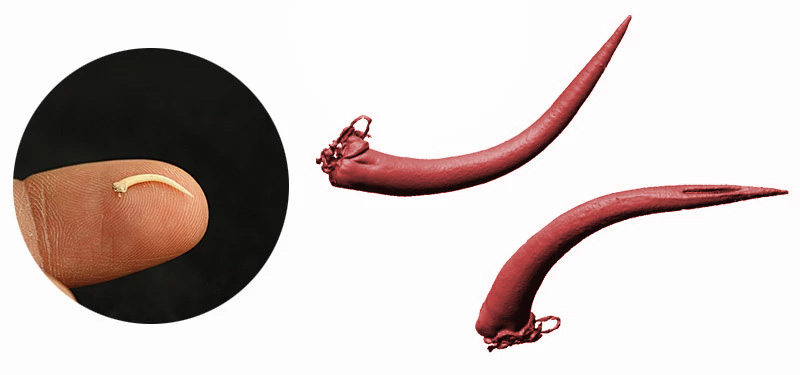
Snake Fang (Credit: MechScan)
Macro / Very Small Objects: When scanning very small objects, the issue lies in capturing fine details. Scanners with a large FOV may not provide the necessary resolution, leading to a loss in detail accuracy. Specialized macro scanners, like Polyga’s C506, are designed for such tasks, offering higher resolution scanning for smaller objects.
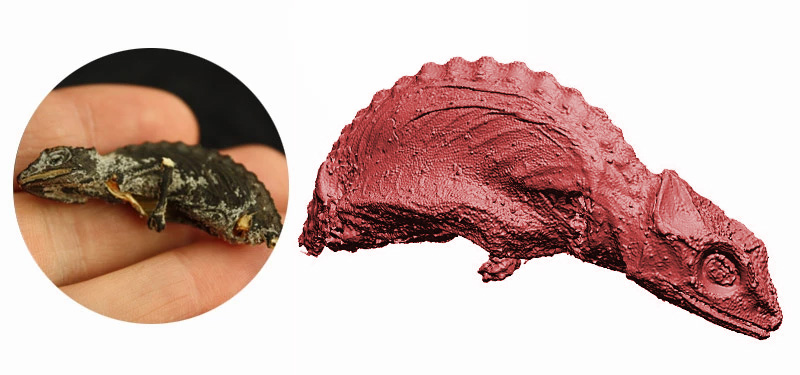
Chameleon (Credit: MechScan)
Small Objects: When scanning smaller objects, the issue lies in capturing fine details. Scanners with a large FOV may not provide the necessary resolution, leading to a loss in detail accuracy. Specialized smaller scanners, like Polyga’s S1 Pro, are designed for such tasks, offering higher resolution for smaller objects.
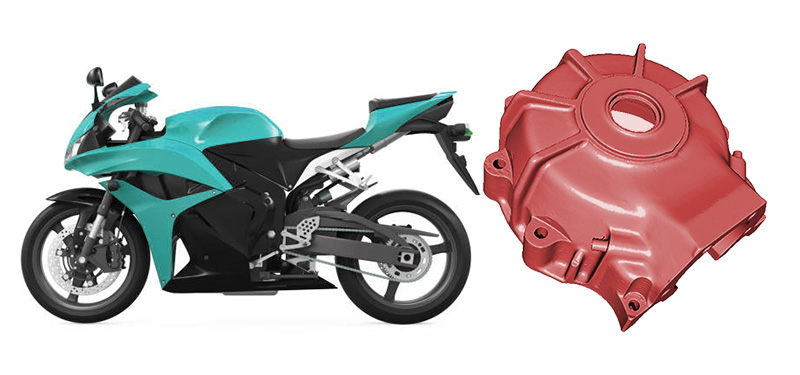
Medium Objects: Additionally, medium-sized objects often have complex geometries or hidden areas that can be difficult to capture fully with a single scan, necessitating multiple scans and complex post-processing to stitch these scans together accurately. These challenges highlight the importance of choosing a scanner with the right balance of FOV and resolution, and the capability to efficiently handle the unique complexities of medium-sized objects.
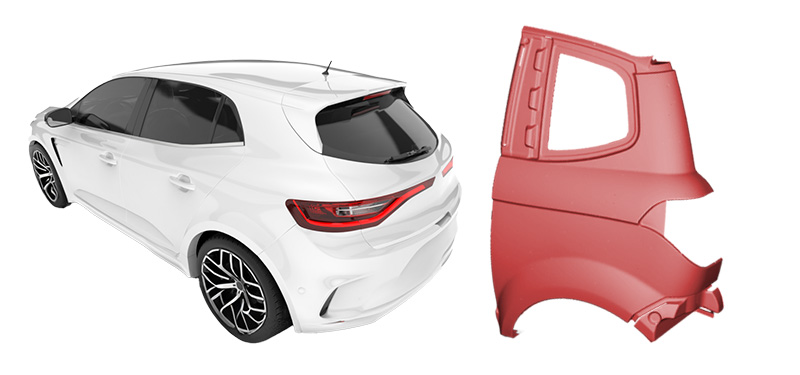
Large Objects: Conversely, scanning large objects with a scanner meant for smaller FOVs can be time-consuming and may result in stitching errors during the post-processing phase. For larger objects, scanners with a wider FOV, like the Polyga L6, are more suitable. However, they may not capture the same level of detail as scanners designed for smaller objects.
See Scan Samples Page
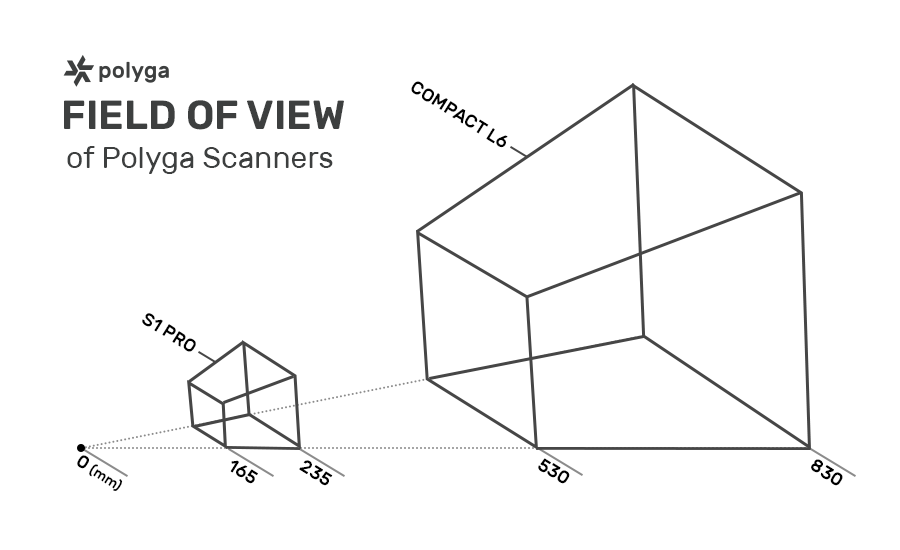
3: Balancing Field of View & Resolution:
The key to successful structured light scanning lies in balancing the FOV with the desired resolution. A larger FOV allows for quicker scanning of big objects but may reduce the level of detail. On the other hand, a smaller FOV increases detail at the cost of scanning time and efficiency. The choice of scanner should be aligned with the primary use case.
4: Overcoming the Size Hurdle:
To mitigate size limitations in structured light scanning, there are several strategies:
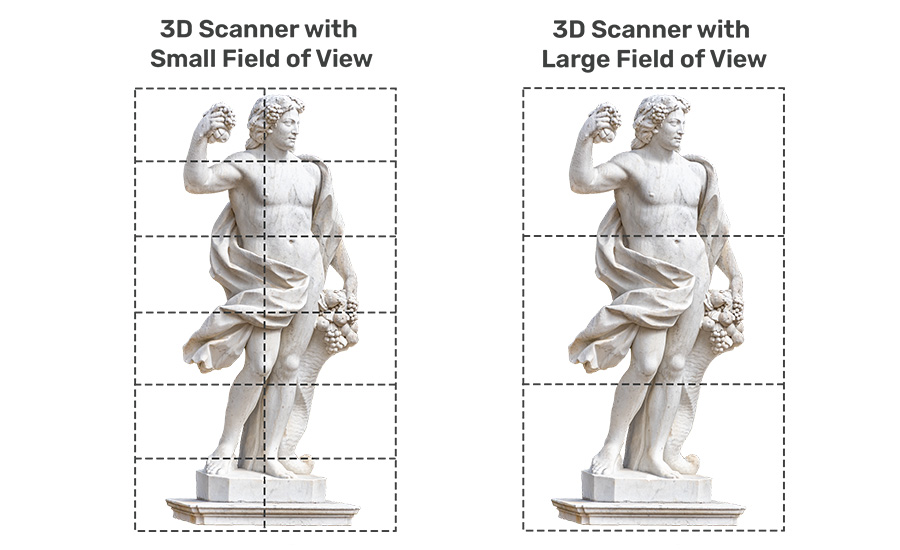
Multiple Scans and Stitching: For large objects, multiple scans from different angles can be stitched together. This approach requires precision and can be time-consuming but results in comprehensive and detailed models.
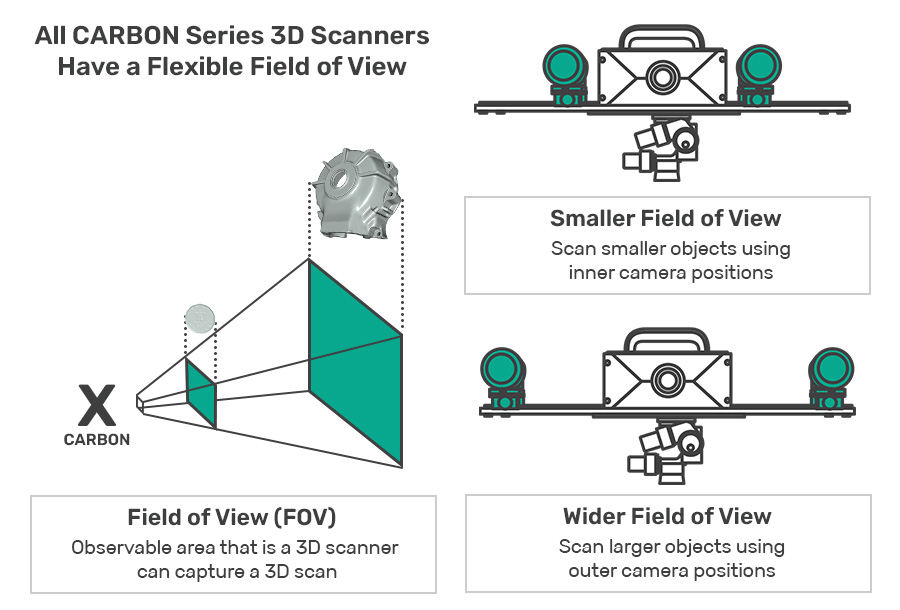
Adjustable FOV: Some advanced scanners offer adjustable FOVs, allowing users to tailor the scanning area to the object’s size. The Polyga Carbon X is an example of a scanner with a flexible FOV, making it versatile for various object sizes
Combining Technologies: For projects requiring both large and small-scale scanning, combining different scanners or integrating structured light scanning with other technologies, like photogrammetry, can offer comprehensive solutions.
Conclusion
While structured light 3D scanning offers remarkable precision and efficiency, understanding its limitations concerning object size is crucial for optimal results. By selecting the appropriate scanner for the task at hand, employing strategies to overcome size constraints, and understanding the trade-offs between FOV and resolution, users can maximize the technology’s potential across various applications.
For further exploration into structured light 3D scanning technologies visit our 3D Scanning Learning Center.
Further Reading
- Part 1 – 3D Scanning 101: Basics of Structured Light
- Part 2 – 3D Scanning 101: Real World Applications of Structured Light
- Part 3 – 3D Scanning 101: Size Limitations of Structured Light
- Part 4 – 3D Scanning 101: Structured Light VS LASER
- Part 5 – 3D Scanning 101: Structured Light VS LiDAR
I hope that this article is helpful to you on your 3D scanning journey.
And, if you have any other questions about what type of scanner is right for your project,
feel free to send them to our sales team at sales@polyga.com, and they will be happy to help.
Best regards,
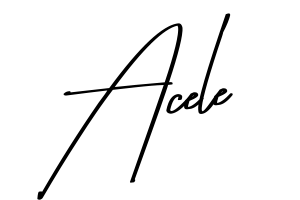
Ace Le
Polyga Inc.
Vancouver, British Columbia, Canada
Email: contact@polyga.com
Website: Polyga.com