Case Study3D Inspection of Large Heavy Machinery Components to Save Material Cost
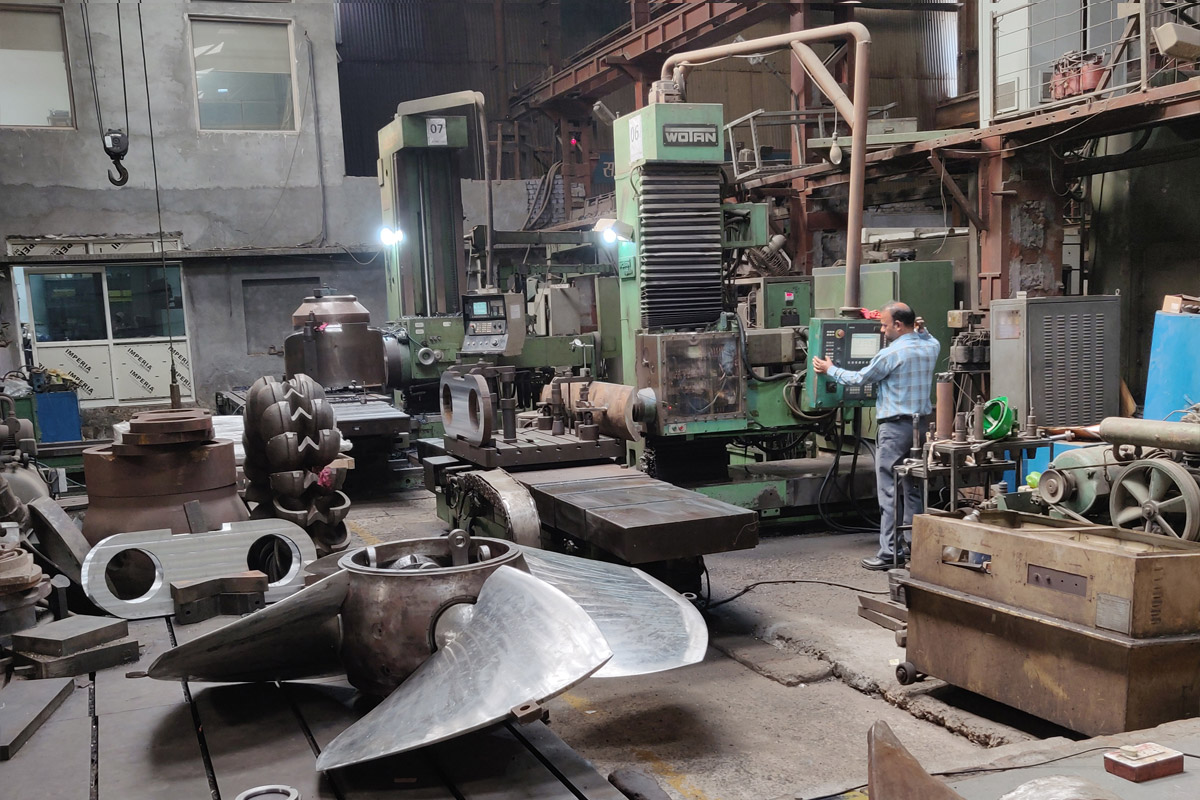
Rasco helped a power plant equipment manufacturer better understand where to reduce raw materials in the production process.
The Challenge
Rasco Automotive Systems is a leading structured-light 3D scanner and service provider specializing in 3D engineering design. A power plant equipment manufacturer enlisted Rasco to optimize its manufacturing process.
The client manufactures heavy engineering equipment for power plants, mainly large impeller blades for power generation equipment. The impellers are first produced as castings and then later machined to the correct specifications.
The raw material used to manufacture these parts is stainless steel. The material is expensive to waste when the casting is machined of excessive material to produce the finished components. Keeping too much raw material on the castings also makes the part heavy for transporting.
How can Rasco help reduce the amount of material waste during the casting process in order to save cost?
Why 3D Inspection?
Inspecting parts using a 3D scanner and 3D inspection software presented the opportunity to identify problem areas and to analyze the part in a comprehensive way. It would quantify where the problem areas exist—eliminating any guesswork and with high accuracy. By taking accurate measurements of the entire surface geometry of the casting using a 3D scanner and then comparing them to the finished machined component using 3D inspection software, Rasco can see the part in its entirety to identify the problem and empower the client to fix these issues.
Solution
The impeller consists of mainly organic surfaces. In this case, using a structured-light 3D scanner provided an easier way to take the most surface measurements in the shortest amount of time, compared to conventional measurement tools (such as calipers or portable CMMs).
Rasco first scanned the stainless steel impeller blade casting using the Polyga Carbon structured-light 3D scanner.
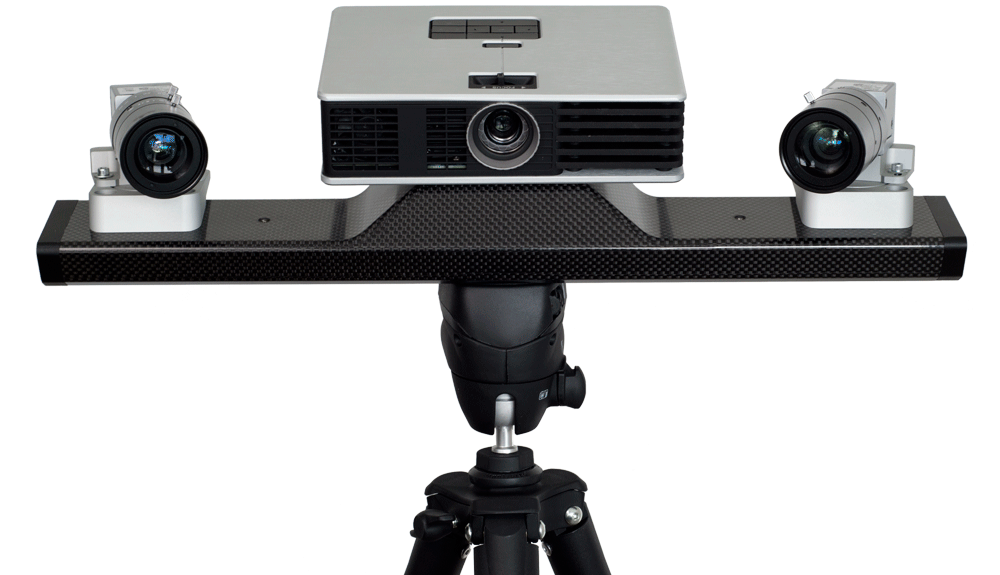
The Polyga Carbon 3D Scanner
The impeller blade is 1500mm x 1000m in size, which is a relatively large component. The Polyga Carbon provided a big field of view for scanning a component of this size while being lightweight and portable to take to the client’s production facility. The 3D scanner is capable of capturing 2+ million measurement data points in 1.2 seconds per scan.
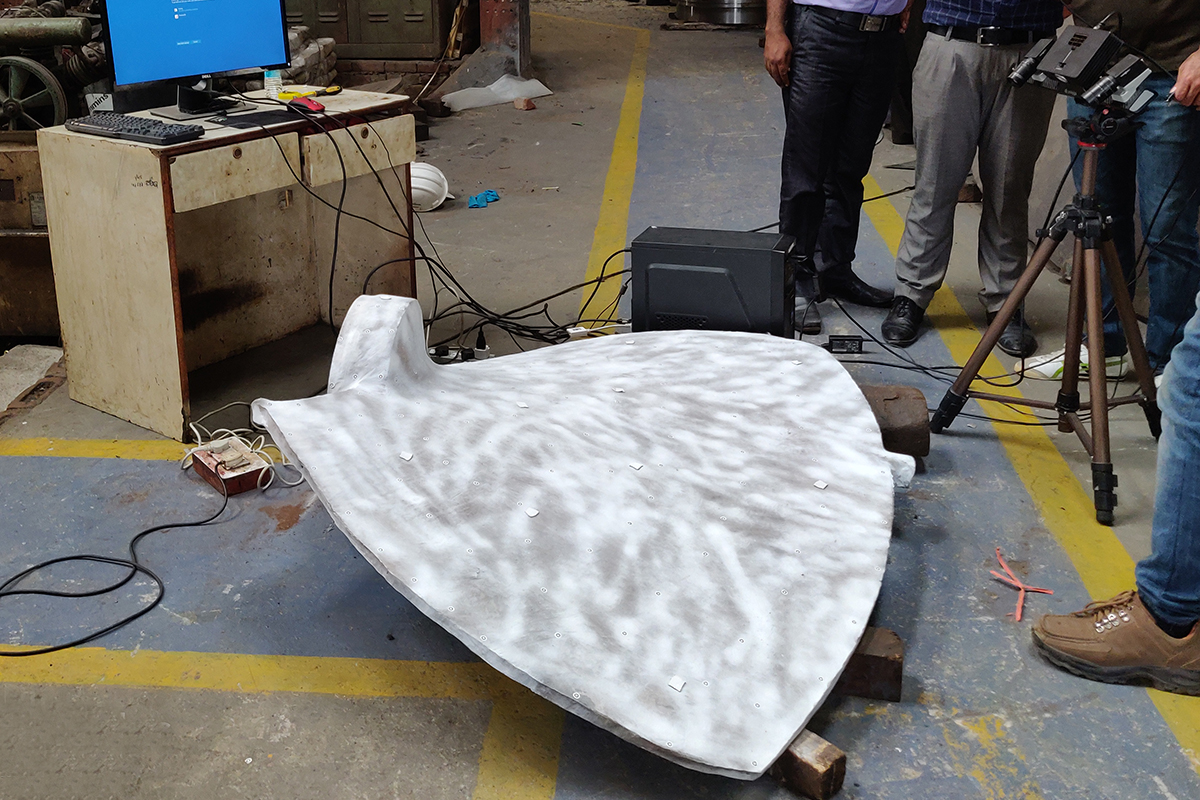
The Polyga Carbon was selected for this project due to having a large field of view and portability.
The use of photogrammetry markers made it fast and easy to scan large organic parts by automating the scanner data alignment process.
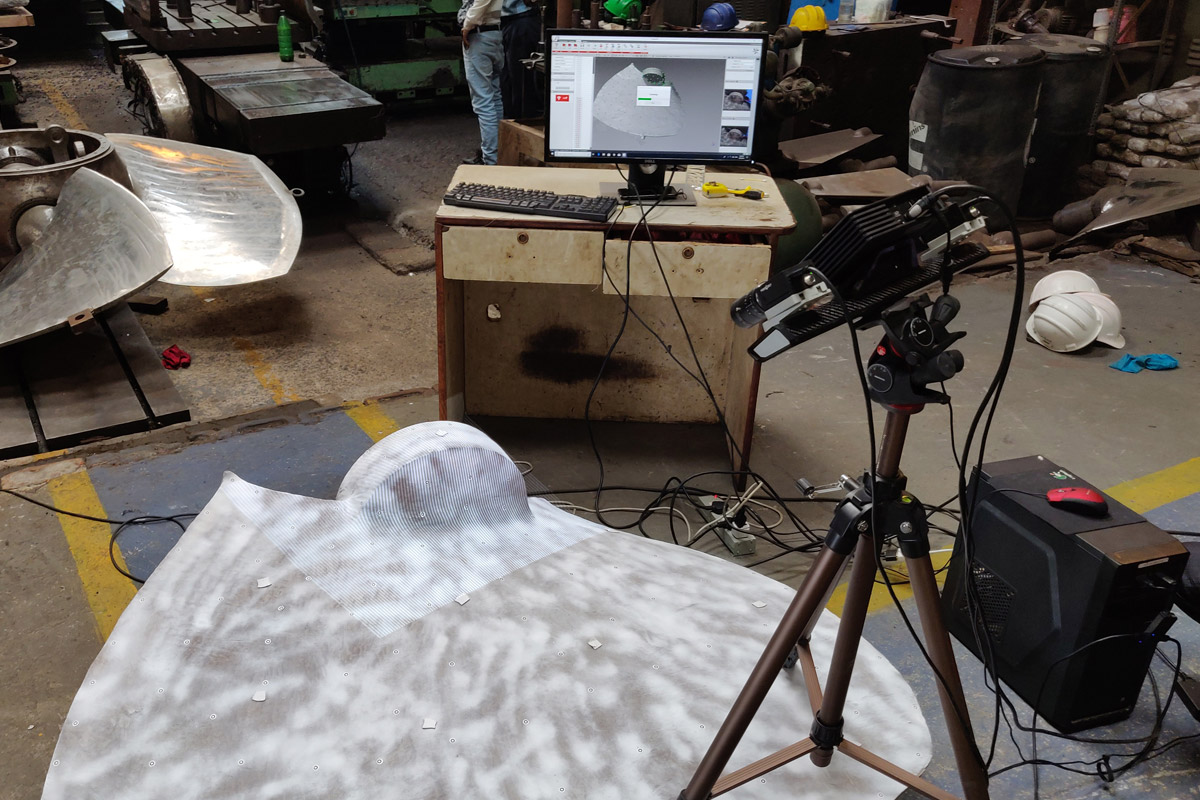
Photogrammetry dots were placed on the impeller to assist in the auto alignment and merging of 3D scans into a complete 3D model.
The impeller casting is digitized into a 3D model once all the scans were captured and merged inside FlexScan3D, a 3D scanning software that powers the Polyga Carbon.
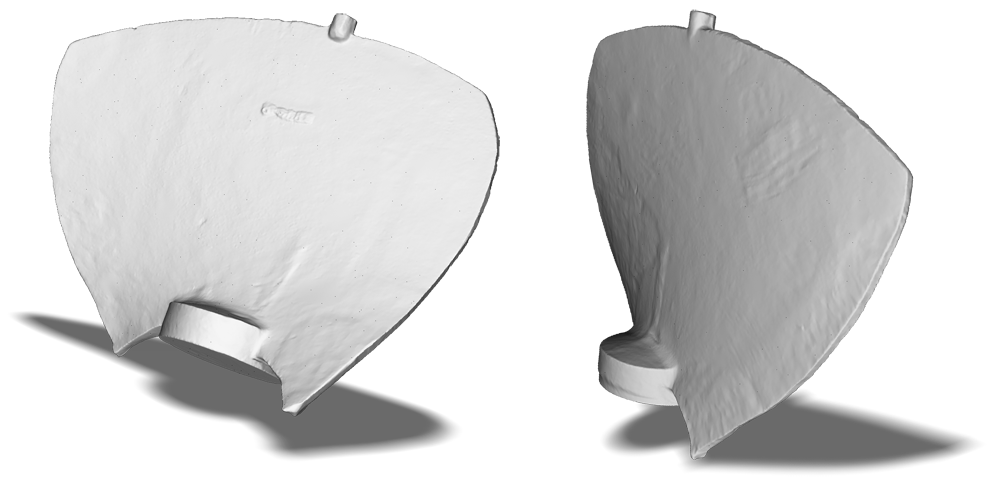
Casting of the impeller as a digital 3D model.
The digital 3D model was compared to the finished machined model in Geomagic Control X to determine if too much material is kept on the casting.
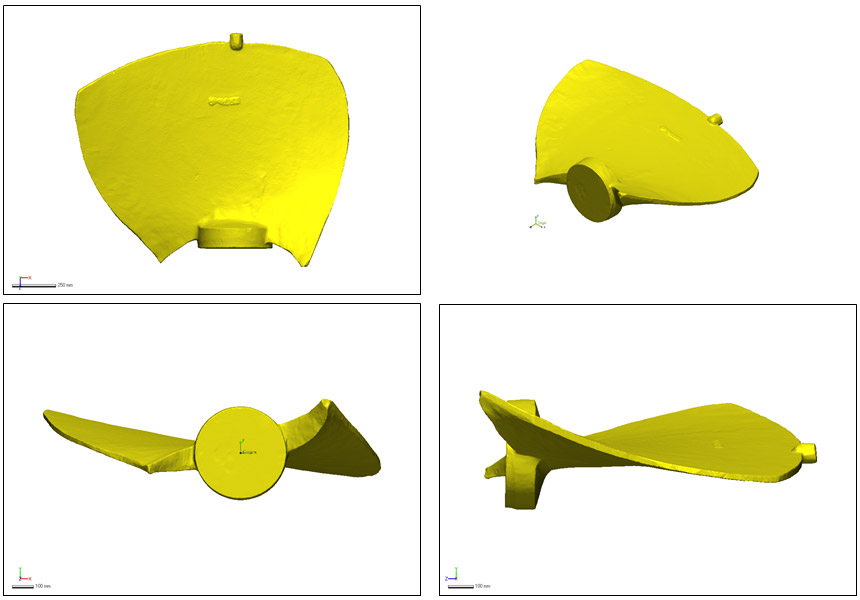
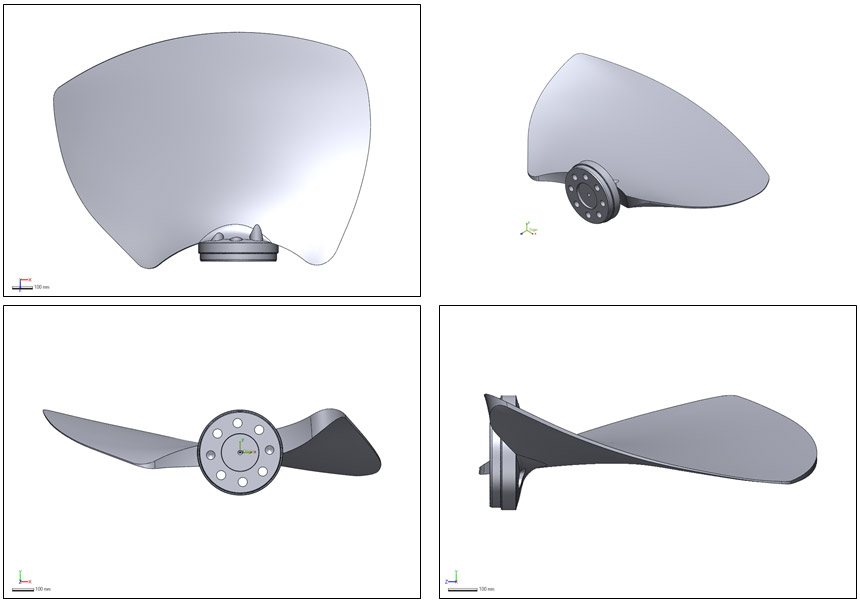
Comparing 3D scan data of the impeller casting to the machined impeller. Measured data (left). Reference data (right).
The reports were autogenerated by Geomagic Control X to pinpoint exactly where the casting has too much material. The diagrams from the report gave a visual understanding of where and how to fix the problem at a glance. The report also provided a thorough analysis to deep dive further into the issue. By reducing materials in these areas, the client is able to increase the overall cost-efficiency of the part.
Visual comparison reports from Geomagic Control X between 3D scanned casting and machined impeller.
Result
The report identified a number of areas where there is much more stainless steel than required. By optimizing the cast component, the current weight of the casting at 819 kg can be reduced to 660 kg. A reduction of 159 kg of raw material translates to approximately $600 USD per component.
Current Casting Weight | Casting Reduced to | Reduce Material By | Cost Savings |
---|---|---|---|
819 kg | 660 kg | 159 kg | $600 USD/per component |
“We are happy with the results of the reports. Inspecting parts using 3D scanning and 3D inspection provided us with the quickest and most accurate way to identify specifically where we can reduce materials. We took corrective actions to reduce excess stock on the casting components that resulted in tremendous material cost savings.”
Rasco’s Client: Director of Quality, Heavy Engineering Equipment Manufacturer